In this article we’ll cover how to calculate cubic yards of excavation and backfill, soil types, excavation equipment, soil testing, compaction, swell factor, the difference between excavating and trenching, and when shoring or trench supports are required.
First let’s cover a few very important items that need to be done before any digging begins.
If you prefer to watch the video of this presentation, then scroll to the bottom.
Call 811 before Digging
The first thing to do is call 811. Calling 811 before digging is crucial because it helps identify and locate underground utilities such as gas lines, water pipes, and electrical cables. This free service coordinates with utility companies to mark the locations of these buried lines, preventing accidental damage that can cause service disruptions, costly repairs, and serious safety hazards such as gas leaks or electrical shocks.
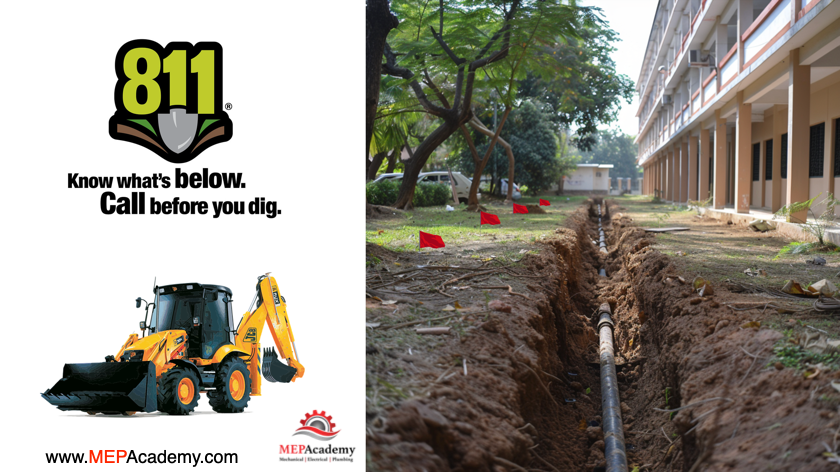
By calling 811, individuals and contractors ensure compliance with safety regulations and protect themselves, their property, and the community from potential dangers associated with unmarked utilities.
APWA Color Coding
Using the American Public Works Association (APWA) color coding system to mark your site before excavating ensures clear and standardized communication of underground utility locations. This system assigns specific colors to different types of utilities, such as red for electric power lines, yellow for gas, oil, or steam, and blue for potable water.
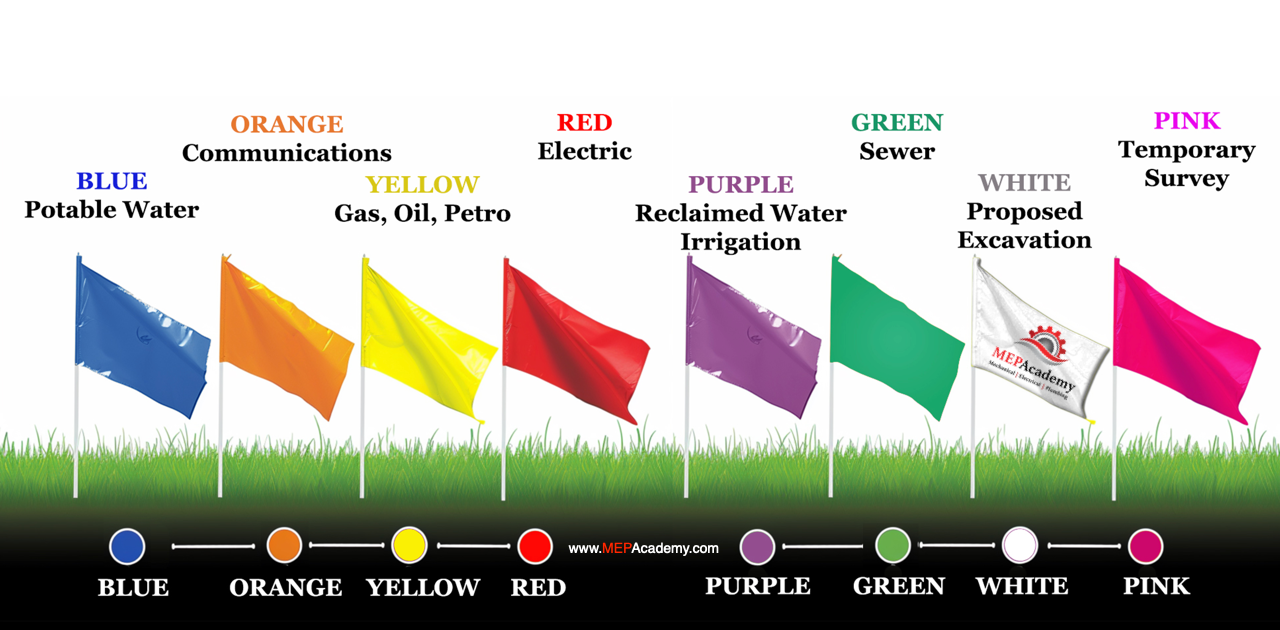
By using these color codes, you help prevent utility damage, reduce the risk of accidents, and comply with industry best practices and regulations, ensuring a safer and more efficient excavation process. A white mark is used to outline the proposed route of the excavation. These markings can be on the surface or with flags and stakes used to increase visibility.
Tolerance Zone
The tolerance zone is a safety buffer zone around existing underground utilities within which excavation must be conducted with extra caution. Typically, it extends 18 to 24 inches (45 to 60 centimeters) from each side of a marked utility line. Within this zone, hand digging or using non-invasive methods like vacuum excavation is required to avoid damaging the utilities. Adhering to the tolerance zone helps prevent utility strikes, ensuring the safety of workers and the integrity of underground infrastructure.
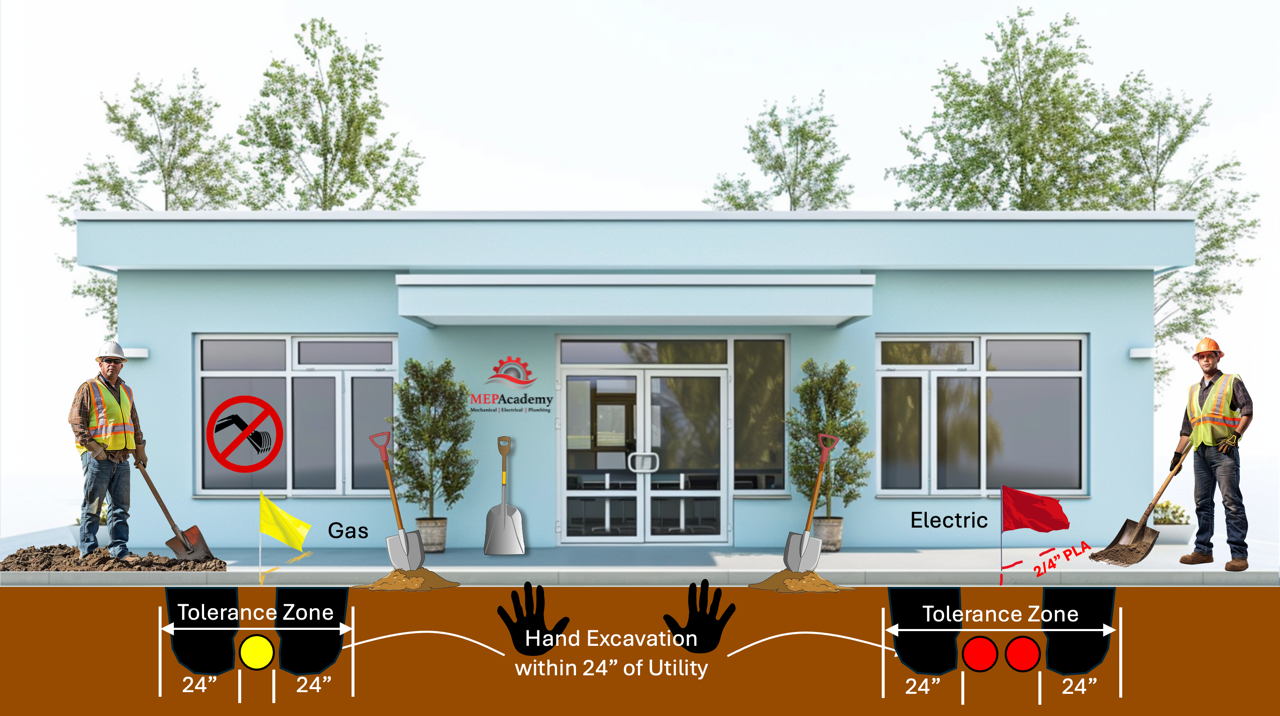
One of the first steps is to determine the Soil type.
Soil Classifications
OSHA (Occupational Safety and Health Administration) classifies soils into three main categories—Type A, B, and C—based on their stability and cohesiveness, which is critical for ensuring safety during excavation work. The soil type must be identified by a competent person as defined by OSHA. Here are the definitions and purposes of these classifications:
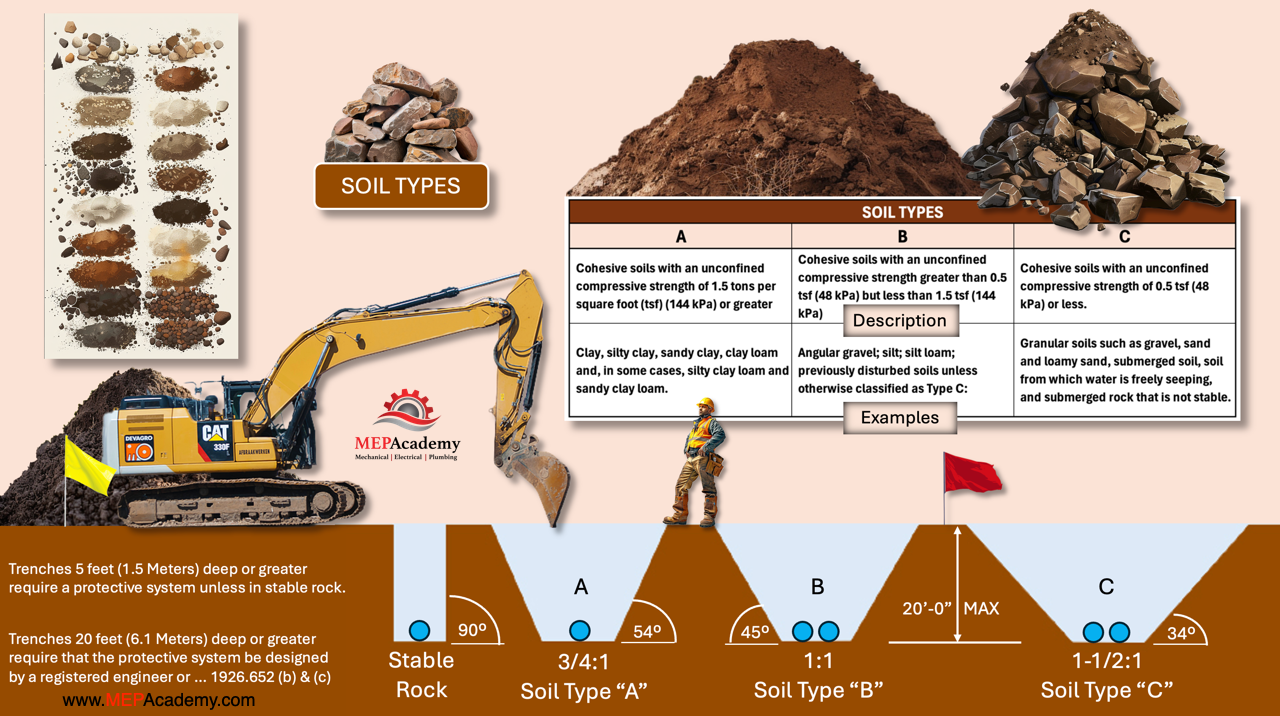
Type A Soil
Type A soil is the most stable and cohesive type of soil. It includes clay, silty clay, and hardpan, with an unconfined compressive strength of 1.5 tons per square foot (tsf) or greater.
Knowing that Type A soil is highly stable helps in planning safe excavation slopes and support systems, minimizing the risk of cave-ins.
Type B Soil
Type B soil has medium stability. It includes silt, silt loam, sandy loam, and previously disturbed soils, with an unconfined compressive strength greater than 0.5 but less than 1.5 tons per square foot.
Understanding that Type B soil is less stable than Type A guides the implementation of additional safety measures such as shoring or sloping at a less steep angle.
Type C Soil
Type C soil is the least stable type. It includes gravel, sand, and loamy sand, with an unconfined compressive strength of 0.5 tons per square foot or less. It also includes submerged soil or soil from which water is freely seeping.
Recognizing Type C soil’s high risk of collapse necessitates the use of the most stringent protective systems, like benching, shoring, or shielding, and sloping the excavation walls at the shallowest angles.
These classifications help ensure that appropriate excavation practices and protective systems are used to maintain worker safety and prevent cave-ins. You can also test the soil.
How to Protect Workers from Cave-ins
Safety is the main concern when working around excavations. There are various protective systems to safeguard workers from cave-ins during excavation and trenching operations. These protective systems are designed to provide support and stability to the excavation walls, reducing the risk of collapse and ensuring worker safety. The primary types of protective systems include:
Sloping
Sloping involves cutting back the trench walls at an angle to create a stable slope that reduces the risk of collapse. The angle of the slope depends on factors such as soil type, excavation depth, and environmental conditions.
Using the Excavation calculator found in the MEP Academy Plumbing Estimating Spreadsheet you can easily calculate the required cubic yards required. Just enter the soil type along with the length, width and depth of the excavation or trench. The calculator takes into consideration the slope if indicated. Just put an “X” in the box for Stable Rock which doesn’t require a slope, or type A soil which is a 3/4:1 slope, type “B” at 1:1, and type “C” soil for 1-1/2:1. The total cubic yards are automatically calculated including any sloped area.
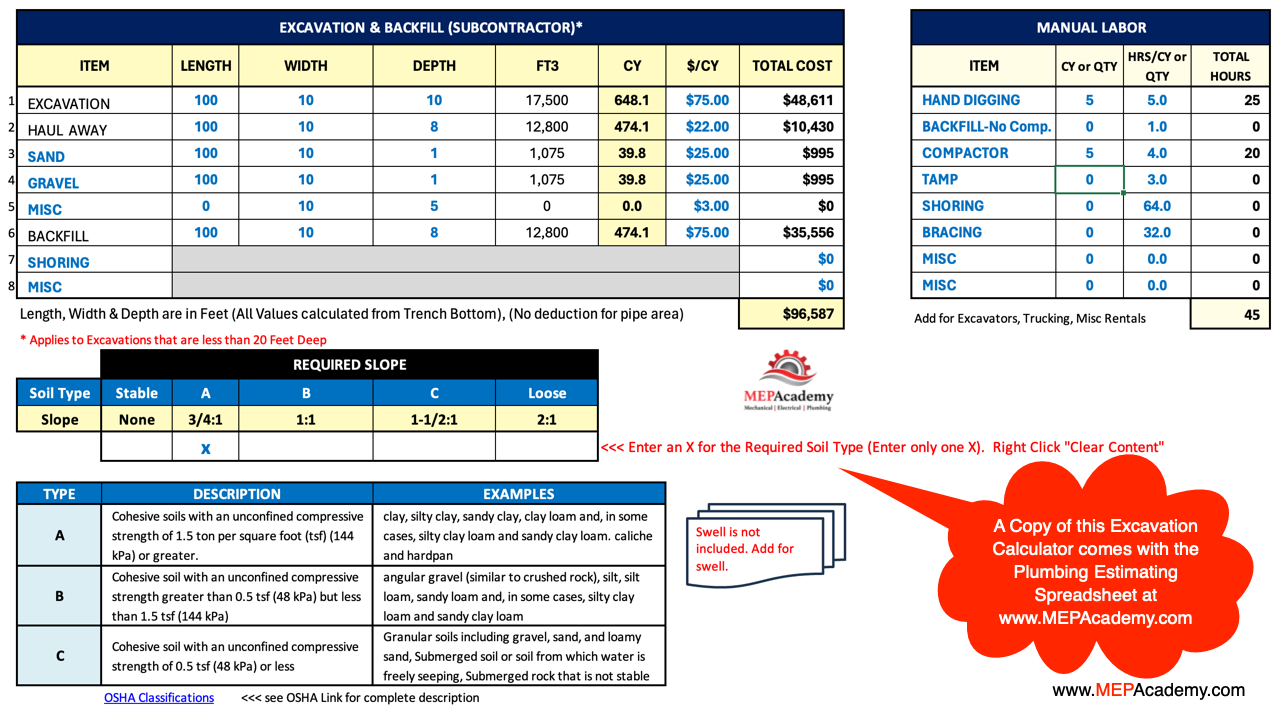
To get a copy of the Estimating Spreadsheet with the Excavation and backfill calculator follow this link. Plumbing Estimating Spreadsheet.
Benching
Single and multiple benching are techniques used to create safe slopes in excavations, particularly in trenches and other large soil removals. These methods help prevent soil collapse and ensure worker safety by reducing the risk of cave-ins. Here’s a description of each:
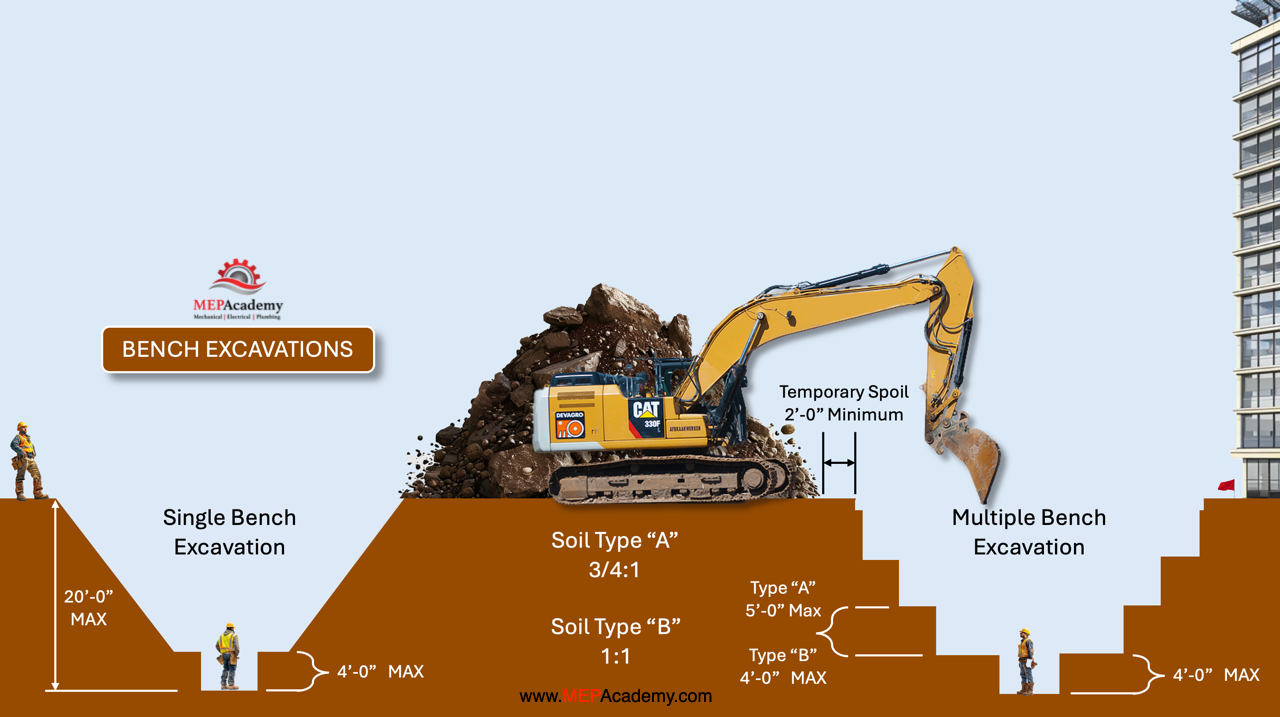
Single Bench
A singe bench involves excavating the soil to create one horizontal step or bench along the slope of the excavation. This bench provides a stable working platform and reduces the steepness of the slope, which helps prevent soil from sliding into the trench.
Single benching is typically used in less deep excavations where the height of the slope does not require multiple steps for stability. It’s suitable for soils that are relatively cohesive and stable.
Multiple Bench
A multiple bench cut involves creating a series of horizontal steps or benches at regular intervals along the slope of the excavation. Each bench acts as a break in the slope, significantly reducing the likelihood of a cave-in by supporting the soil above it.
Multiple benching is used in deeper excavations where a single bench would not provide sufficient stability. It is especially important in less cohesive soils that are more prone to collapse. This method ensures greater safety by distributing the weight of the soil and providing additional support.
Key Considerations
As a general rule, the bottom vertical height of the trench must not exceed 4 ft (1.2 m) for the first bench. Subsequent benches may have a vertical height of up to 5 ft (1.5 m) in Type A soil and 4 ft (1.2 m) in Type B soil, reaching a total trench depth of 20 ft (6.0 m).
Slopes vs Trenches
To avoid the need for a sloped excavation, which can be impractical in certain situations due to space constraints or other factors, several alternative protective systems can be used to ensure worker safety and prevent cave-ins. Trenches 5 feet (1.5 meters) deep or greater require a protective system unless the excavation is made entirely in stable rock. If less than 5 feet deep, a competent person may determine that a protective system is not required. The alternatives to sloping include these trench options:
1. Shoring Systems:
Hydraulic Shoring: Uses hydraulic pistons to apply pressure to trench walls, holding them in place. It’s adjustable and can be quickly installed and removed.
Mechanical Shoring: Involves using metal supports such as screw jacks, struts, and beams to brace trench walls. These systems are strong and can be tailored to the specific dimensions of the trench.
Pneumatic Shoring: Similar to hydraulic shoring but uses air pressure to stabilize the trench walls.
2. Trench Boxes
Trench boxes are robust steel or aluminum structures placed inside the trench to protect workers from cave-ins. They provide a safe working area within the trench and are particularly useful for deep or narrow trenches.
Trench boxes come in various sizes and configurations to suit different excavation needs and can be stacked for deeper excavations.
3. Shield Systems:
Shield systems are portable, protective structures that can be moved along the trench as work progresses. They can be made of steel, aluminum, or composite materials and offer flexibility in terms of size and strength.
Examples include slide rail systems, which provide support to the trench walls as the excavation proceeds.
We have shown you three protective system and there are many others available.
Using these protective systems allows for vertical or near-vertical trench walls, which can be critical in areas with limited space or where traditional sloping is not feasible. The choice of system depends on factors such as soil conditions, trench depth, available space, and project-specific requirements. Each method provides a safe working environment for workers and ensures compliance with OSHA regulations and industry safety standards.
When is Shoring Required
Shoring is required during excavation or trenching when the soil’s stability is compromised, posing a risk of collapse or cave-in. Here are common scenarios when shoring is necessary:
Unstable Soil Conditions
Shoring is essential when excavating in soil types prone to collapse, such as loose or granular soils (Type C soils according to OSHA classification). These soils lack cohesion and are at a higher risk of cave-ins without support.
Deep Excavations
As the depth of the excavation increases, the lateral pressure exerted by the surrounding soil also increases. Shoring becomes necessary to prevent the walls of the trench from collapsing inward under the pressure, ensuring the safety of workers.
Adjacent Structures
When excavating near existing structures, utilities, or roads, shoring may be required to prevent soil movement that could damage adjacent infrastructure. Shoring also provides stability to the excavation site, minimizing the risk of ground settlement or subsidence.
Water Table
Excavations conducted below the groundwater table are susceptible to water seepage and soil instability. Shoring is necessary to prevent water infiltration and maintain the integrity of the excavation walls, especially in cohesive soils that may become saturated and lose strength.
Changing Soil Conditions
Soil conditions can change unexpectedly during excavation due to weather conditions, groundwater fluctuations, or disturbances from nearby activities. If soil stability becomes compromised, shoring may be required to ensure the safety of workers and prevent accidents.
Regulatory Requirements
Local regulations and safety standards may dictate when shoring is required based on factors such as excavation depth, soil type, and proximity to existing structures or utilities. Compliance with these regulations is essential to ensure safe excavation practices.
In summary, shoring is necessary during excavation or trenching operations to provide support and stability to the excavation walls, reducing the risk of collapse and ensuring the safety of workers and surrounding infrastructure.
Soil Compaction
Compaction refers to the process of densifying the soil or backfill material to increase its load-bearing capacity and prevent settling or shifting over time. After plumbing pipes or structures are placed in the excavated trenches, the backfill material is added in layers and each layer is compacted using mechanical means such as vibratory plate compactors, rollers, or tampers. Proper compaction ensures that the soil is stable and that voids are minimized, which helps to protect the integrity of the plumbing infrastructure, preventing future issues such as pipe displacement or leaks due to ground movement.
Swell Factor
Swell refers to the increase in volume that soil or excavated material undergoes when it is disturbed and removed from its natural, compacted state. When soil is excavated, it expands because the tightly packed particles are loosened, resulting in an increase in volume. This phenomenon is known as swell.
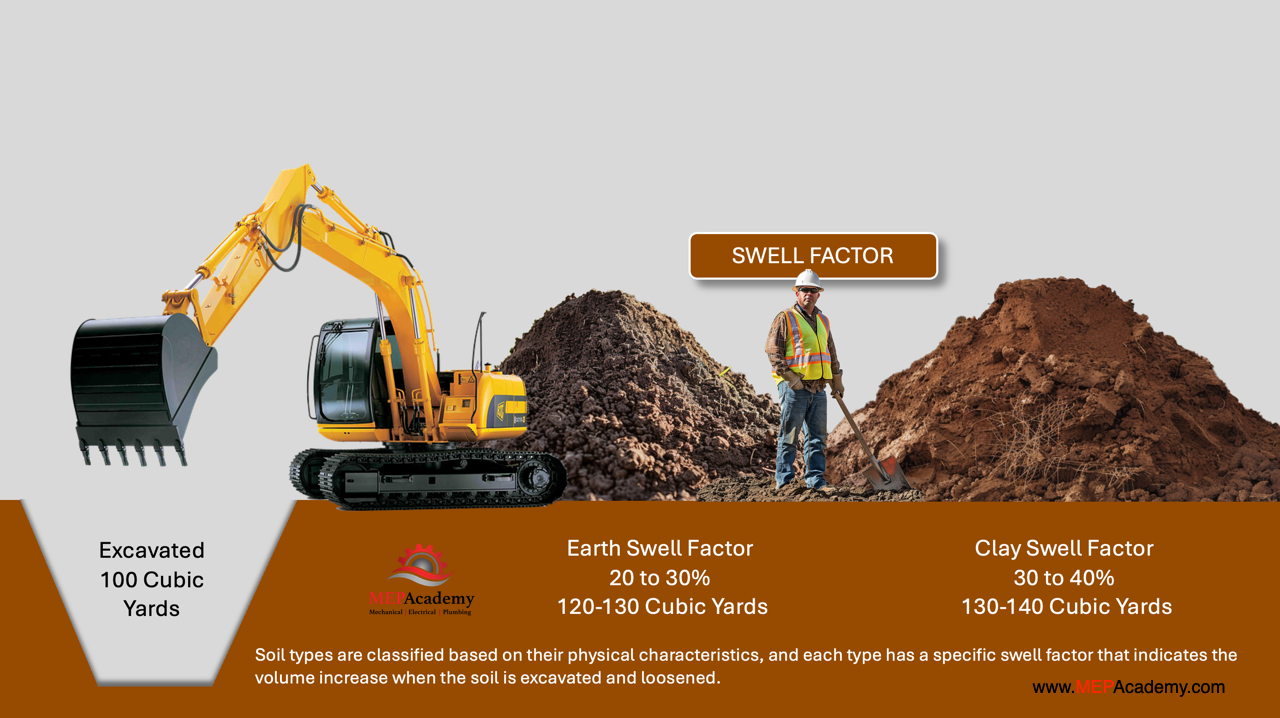
Understanding swell is important for plumbers and construction professionals because it affects the amount of backfill material that will be required to refill an excavated trench or hole. Proper planning for swell ensures that there is sufficient material to achieve the desired compaction and stability when backfilling around plumbing installations.
Sand and Gravel Bedding
Using sand and gravel at the bottom of an excavation where piping is being installed serves several important purposes:
Providing a Stable Bedding:
Sand and gravel create a stable and even bedding for the pipes, ensuring that they are well-supported along their length. This reduces the risk of pipe deflection or damage due to uneven settlement or point loading.
Facilitating Drainage:
Sand and gravel promote good drainage around the pipes, preventing water accumulation that could lead to soil instability or erosion. Proper drainage helps maintain the integrity of the piping system and prevents issues related to waterlogging or frost heave.
Protecting Pipes from Sharp Objects:
Sand and gravel act as a cushion, protecting the pipes from sharp rocks or other debris in the soil that could puncture or damage them. This is particularly important for plastic or PVC pipes, which are more susceptible to damage from sharp objects.
Easing Piping Installation:
The granular nature of sand and gravel makes it easier to achieve precise grading and alignment of the pipes during installation. This ensures that the pipes are laid at the correct slope and elevation for optimal performance.
Amount of Sand and Gravel Used
The amount of sand and gravel used at the bottom of an excavation varies depending on the type and size of the piping, as well as the project specifications. However, typical guidelines include:
Bedding Layer:
A bedding layer of sand or gravel is usually placed 4 to 6 inches (10 to 15 centimeters) thick. This layer provides a firm foundation for the pipes.
Initial Backfill:
After the pipes are laid, an initial backfill of sand or gravel is placed around and over the pipes to a depth of about 6 to 12 inches (15 to 30 centimeters) above the pipe. This initial backfill helps to secure the pipes in place and provides additional protection.
Final Backfill:
The final backfill, which may consist of the excavated soil or other suitable material, is then placed on top of the initial backfill. The final backfill is typically compacted in layers to prevent settling and ensure stability.
These layers help ensure that the pipes are properly supported, protected, and aligned, contributing to the longevity and functionality of the piping system. The exact specifications may vary based on local codes, engineering requirements, and the specific conditions of the project site.
Digging Equipment used for Excavations and Trenches
Excavations and trenches require specialized equipment to efficiently and safely remove soil and create the desired shapes and depths. Here are various types of digging equipment commonly used for these purposes:
Excavators
Excavators are versatile machines equipped with a bucket attached to a hydraulic arm. They can rotate 360 degrees and are capable of digging, lifting, and loading materials.
Excavators are suitable for a wide range of excavation tasks, including digging trenches, foundations, and utility trenches.
Backhoe Loaders
Backhoe loaders combine a backhoe (rear-mounted digging arm) with a loader (front-mounted scoop). They are versatile and commonly used in construction projects.
Backhoe loaders are useful for smaller excavation jobs, such as digging trenches for utilities, backfilling, and loading materials.
Trenchers
Trenchers are specialized machines designed specifically for digging narrow and deep trenches. They feature a rotating chain or blade that cuts into the ground to create the trench.
Trenchers are ideal for excavating trenches for utilities like water pipes, sewer lines, and electrical conduits.
Mini Excavators
Mini excavators are compact versions of standard excavators, with a smaller footprint and reduced weight. They offer increased maneuverability and are suitable for tight spaces.
Mini excavators are commonly used for small-scale excavation projects, landscaping, and utility installation in urban areas or confined spaces.
Crawler Excavators
Crawler excavators are equipped with tracks for stability and mobility over rough terrain. They offer high digging power and are suitable for heavy-duty excavation work.
Crawler excavators are used in large-scale excavation projects, such as road construction, mining, and earthmoving.
Skid Steer Loaders
Skid steer loaders are compact, maneuverable machines with a small turning radius. They feature a bucket or attachment mounted on a pivoting frame.
Skid steer loaders are versatile and can be used for various tasks, including excavation, loading, grading, and landscaping.
These are just a few examples of the equipment used for excavations and trenches. The choice of equipment depends on factors such as the size of the project, the type of soil, accessibility, and the specific requirements of the task at hand.
Plumbing Estimating Spreadsheet with Excavation Calculator