Chillers are used to cool buildings by circulating chilled water through a system that absorbs heat and removes it from the space. They rely on refrigerants to facilitate the cooling process, but if these refrigerants leak into the chiller room, they can pose serious health and safety risks due to potential toxicity or displacement of oxygen. To mitigate this hazard, refrigerant monitors are installed to detect leaks early, ensuring a safe environment for personnel and preventing dangerous exposure.
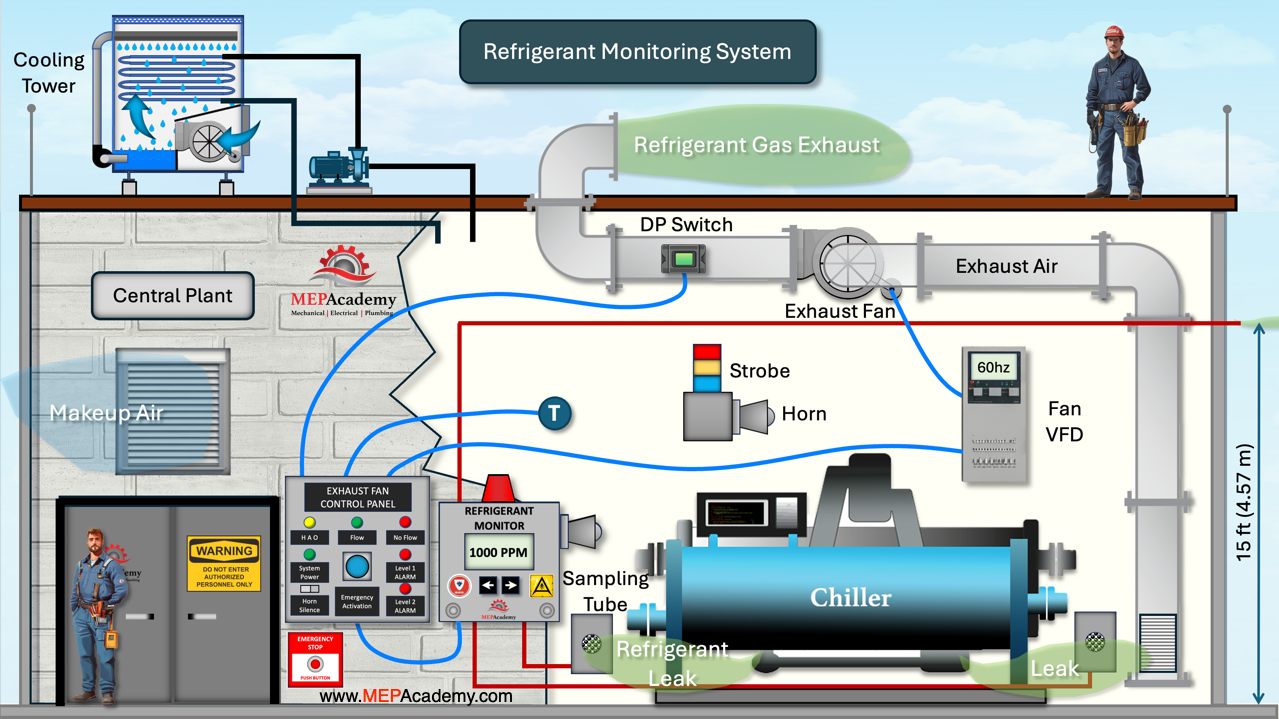
The refrigerant monitor has refrigerant sensors which should be positioned near potential leak points such as chiller units, refrigerant piping joints, and valve stations. Since different refrigerants have varying densities, sensor height plays an important role. Heavier-than-air refrigerants, such as R-123, necessitate sensor installation closer to the floor, typically between 12 to 18 inches above ground level.
Sample tubing used in refrigerant monitoring systems must be carefully installed to prevent contamination and ensure longevity. Exhaust tubing must be routed to a well-ventilated outdoor area to prevent refrigerant buildup within the facility. The length of these tubing runs should be minimized to ensure faster response times and more accurate leak detection results.
Next the chiller room will need an exhaust fan to be activated during a refrigerant leak. The chiller room exhaust fan plays a crucial role in maintaining proper ventilation and air quality. In larger chiller rooms, it typically operates between two speeds with the use of a VFD.
Ventilation System
Refrigeration machinery rooms must have dedicated mechanical exhaust systems to ensure proper ventilation and safety. These exhaust systems are essential for removing potentially hazardous refrigerant leaks, maintaining air quality, and preventing dangerous temperature buildup inside the room.
Minimum Ventilation Requirements
When the machinery room is occupied, the ventilation system should operate at minimum speed or at a rate of at least 0.5 cubic feet per minute (CFM) per square foot of room area (2.54 Liters per square meters) or 20 CFM (9.4 liters per second) per person present, whichever is greater. This ensures that fresh air circulates adequately, preventing the accumulation of refrigerants or other harmful gases. The requirement helps maintain safe breathing conditions for personnel working in the room.
Temperature Control Considerations
The exhaust system must also function to regulate the room’s temperature, preventing excessive heat buildup from equipment operation. Specifically, the fan should run at full speed if the temperature in the room exceeds the setpoint in order to maintain temperature conditions inside that does not exceed:
- 18-degree Fahrenheit (10 degree Celsius) above the temperature of the incoming air, or
- A maximum room temperature of 122-degrees Fahrenheit (50 degrees Celsius), whichever is higher.
Another code states the ventilation or mechanical cooling systems shall provide a temperature of not more than 104 degrees Fahrenheit (40 degrees Celsius) in the chillers mechanical room under design load and weather conditions.
This requirement ensures that mechanical equipment does not overheat, reducing the risk of system failures, fire hazards, or unsafe working conditions for technicians. By maintaining proper airflow and temperature control, the ventilation system improves equipment efficiency, extends system lifespan, and enhances worker safety. Check the local code for the specific requirements for the location of your building.

Refrigerant Alarm
For our example let’s say that the first level of alarms is set to activate if the refrigerant level exceeds 500 parts per million. This will send a message to the fan to run at full speed, pulling air in through the exhaust air grille located 12 inches (30 centimeters) off the floor. A digital signal can be sent to the strobe light to activate the amber color for a warning. The technician can then search for a leak. Different refrigerants will have different alarm levels, such as R123 may have level one alarm set at 25 parts per million and level two alarm set at 50 parts per million,
The second set of alarms will be activated if the refrigerant continues to increase and reaches 1,000 parts per million at which point the strobe light will start flashing and the horn will sound. Also, at the second level of alarms a signal can be sent to shut down all equipment related to the refrigeration equipment such as compressors and chillers with their pumps.
The mechanical room personnel should immediately exit the chiller room. ASHRAE standard 15 section 8.11.5 has the required calculation for the volume of exhaust air that needs to be provided during an emergency purge based on the mass of refrigerant in the largest system.
The exhaust fan runs at full speed whenever the room temperature exceeds setpoint, the emergency break-glass switch is activated, and if a level one or level two alarm is reached.
Flow and No-Flow Indicators
A Differential Pressure Sensor sends a signal to the ventilation panel indicating one of two condition, flow or No-Flow.
Makeup Air
When exhausting air, it’s important that the fan isn’t starved for air by providing a makeup air louver to bring in fresh air as the fan is running. The louver should be located to provide optimum air movement through the chiller room to the exhaust inlet to remove any leaked refrigerant.
The refrigerant monitor sends a signal to the Ventilation Fan Controller indicating the need for the fan to speed up because of the detection of a minimum level of refrigerant. The controller sends an analog signal to the fans VFD to increase the fans speed as programmed. There will also be a digital signal for starting and stopping the fan. If the refrigerant leak reaches level 2 values in the space the refrigerant monitor sends a digital signal to activate the audio and visual alarms inside the chiller room and outside at the entrance to the room per ASHRAE 8.11.2.1
Break-glass On-Only Control Switch
The exhaust fan requires a break-glass on-only control switch located immediately outside the chiller room door to ensure emergency ventilation in the event of a refrigerant leak. This setup allows personnel to quickly activate the exhaust system without entering a potentially hazardous environment. Since many refrigerants are heavier than air and can displace oxygen, an uncontrolled leak inside the chiller room can create a life-threatening situation. The on-only function ensures that the fan remains running until the area is confirmed safe, preventing accidental deactivation. This safety measure is critical for protecting workers, preventing refrigerant buildup, and complying with ventilation codes in mechanical rooms.
Emergency Off-Only Control Switch Requirements for Chiller Rooms
To ensure safety in refrigeration machinery or chiller rooms, an emergency off-only control switch must be installed immediately outside the primary exit of the room. This switch must be of a break-glass type or have a protective cover, preventing accidental activation while ensuring quick access in an emergency. This requirement applies regardless of the refrigerant type or electrical system used in the installation.
The primary function of this emergency switch is to shut off critical refrigeration equipment inside the machinery room and activate audio and visual alarms. This includes:
- Refrigerant compressors, which circulate refrigerant through the system.
- Refrigerant pumps, which help move liquid refrigerant within the system.
- Normally closed automatic refrigerant valves, which control the flow of refrigerant.
By shutting down these components, the switch helps prevent continued refrigerant leakage or system overpressure, reducing potential hazards.
Additionally, the emergency control system is designed to automatically shut off refrigeration equipment if the concentration of refrigerant vapor in the room exceeds safe limits. Specifically, the system will activate when the vapor detector reads a level that is:
- Above the detector’s upper detection limit, or
- At 25% of the refrigerant’s lower flammability limit (LFL), whichever is lower.
This automatic shutdown feature is crucial in preventing toxic exposure, oxygen displacement, or fire risks, ensuring a safe environment for personnel and protecting the facility from potential refrigerant-related hazards.
These are the basic components of a refrigerant monitoring system. There are many variations on this layout and the requirements can vary by the code authority where the property is located.