Chapter #4 – Sheet Metal Field Labor Productivity
After your reports have finished running on the estimating computer software program its time to review the field labor. If you don’t have a computer estimating software program then your all your field labor numbers would be generated using Excel or some other spreadsheet totaling software. Hopefully your estimating software has the capability to breakdown the labor reports for easy analyses.
We will want to look at the labor productivity, meaning how many linear feet of ductwork is being installed per man-day (LF/MD) as one of the methods of labor analysis, or linear feet per hour (LF/HR) if you want to look at it in a micro sense. A man-day is equivalent to an 8-hour day.
Another method of labor analysis is hours/piece (Hrs/Pc) and pounds/hour (Lbs/Hr). When we took the sheet metal off we separated our takeoff into different zones and systems. At this point we would analyze each zone and system separately.
There is no better way to review the productivity of your project, except to go through it line by line as grouped per your System and Zone descriptions. This will help those in the estimating review to build the job in their head, giving everyone involved a good sense of the project. If you apply a factor overall to everything, no one will fully grasp the project as deeply as a thorough review would allow. Some companies do just that—they apply one factor to all the labor based on the type of project.
We will first cover some of the factors that affect productivity. This is often one of the most difficult undertakings of an estimator, the analysis and adjustment of labor for non-typical conditions. If using a computer estimating program with SMACNA labor units, then you would be adjusting from a 1.0 of SMACNA labor.
Measuring Labor Productivity
This is one of the main duties of the sheet metal estimator, as it has the greatest impact on cost. Labor proposes the highest risk to the contractor, as it is one of the greatest variables. The cost for other aspects of the bid, such as material, equipment and subcontracts shouldn’t vary much from their original bid time cost, unless an error was made.
But labor will vary from your assumptions at bid time about how productive the field labor would be able to install the required equipment and material. So it is labor that really needs to be understood in order to provide accurate estimate that will return a reasonable profit for the owners.
SMACNA Labor Benchmark
There are various organizations that publish labor productivity values for the HVAC Sheet Metal industry including SMACNA, the Sheet Metal and Air Conditioning National Association. There are various factors affecting the productivity of labor from some baseline, or benchmark standard. Each project presents various challenges based on differing site conditions. Labor needs to be adjusted from the standard benchmark labor units to match the specifics of the project under consideration.
Most often labor is the riskiest portion of the estimate because of the assumptions made on the productivity that the project is assumed to be able to redeem. SMACNA provides three progressive categories of labor risk, “Normal”, “Difficult”, and “Very Difficult”. As the conditions worsen, the corresponding labor cost will increase. If you are bidding a retrofit project, one in where you are working in an existing building, then SMACNA considers all remodels to be categorized as either “Difficult” or “Very Difficult”.
SMACNA Labor Tables (Database)
If you are using the SMACNA Reference Manual for Labor Units for your field labor productivity then you will apply a factor to align the SMACNA labor with your field labor feedback (Historical Data), if your company maintains such information. SMACNA labor tables were original assembled from a survey of over 300 member firms from the United States and Canada.
The labor units contain 138 tables for the fabrication and installation unit labor values for the installation of ductwork, fittings, hangers, equipment and accessories. Labor units are available in pounds per hour, or hours per piece, in addition to labor for equipment based on the size of the HVAC equipment.
The SMACNA labor units exclude engineering, supervision, field layout (Detailing) or non-standard construction.
You can use the SMACNA labor units that are embedded in your estimating software if you have one, or you could purchase the SMACNA labor units Excel version, that allows you to adjust values using their spreadsheet. The electronic Excel spreadsheet allows you to rate your project in 30 different difficulty categories in an effort to provide you with the difficulty factor of your project compared to a standard project. There are three project difficulty ratings based on the information you enter for your project, indicated as “normal”, “difficult”, or “very difficult.”
Labor Feedback
The best way to determine how much labor is required for a particular task of work, is to review historical data, that is what it took your companies field crew in hours to perform similar work that has already been completed.
If you are fortunate enough to work for a company that tracks their labor, then you will have a labor database to review when assembling an estimate. The database accumulated from labor feedback will give you a reference for how long it takes to install various materials and equipment, depending on the sophistication and accurate tracking and reporting of the labor spent.
Historical data should be used as a guide for your current project, but not without serious consideration for the differences in the respective projects. Just as SMACNA rates the different categories of labor according to their difficulty, you must know under what conditions your historical database reference project labor was installed under. Understanding what effects labor is the first place to begin before any adjustments up or down from a benchmark labor database is performed.
Industry Labor Database vs Historical Data
There are two main ways to bid labor on a project. The first is to use an industry labor database, and the other is to use some form of historical labor feedback from completed projects. The third way is to use a hybrid of the two. Do your takeoff using the industry standard database, such as SMACNA labor units, and then adjust the productivity according to your historical labor.
The most accurate labor productivity is going to be based on the feedback you received from the field on jobs completed that are similar to the one you are currently proposing, making adjustment for any differences. Let’s look at a few ways to record and adjust labor in the field.
Sheet Metal Labor Productivity Units
There are several methods for analyzing labor productivity for any project. You need to find one that you are comfortable with and that matches the specifics of your company. We will cover four methods of measuring labor productivity.
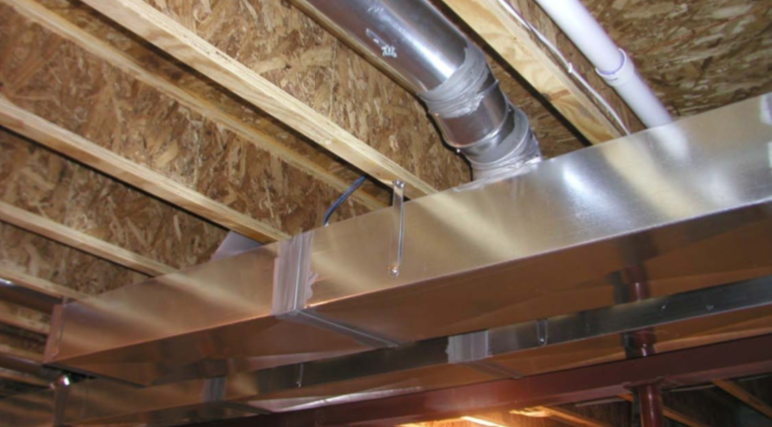
Labor can be measured in LF/MD (linear feet per man day), which means that so many feet of duct can be installed in an 8 hour period, the same unit can be defined as LF/HR (linear feet per hour), which means how many feet can be installed in one hour.
Some contractors like to look at LBS/HR, which means how many pounds of sheet metal that can be installed in an hour. And then there is the HRS/PC (hours per piece), which is defined as how many hours it takes to install a piece of duct or fitting.
MD = 8 hours
- LF/MD = Linear feet per man day
- LF/HR = Linear feet per hour
- LBS/HR = Pounds per hour
- HRS/PC = Hours per piece
Linear Feet Per Hour (LF/HR) & Linear Feet Per Man Day (LF/MD)
Ft/MD (Feet per Man Day) is used as a measurement of the labor productivity for a certain ductwork system. If your labor feedback from previous projects indicates that you can install rectangular main ducts at 25 LF/MD (linear feet per man day), then you would apply this productivity factor to the total linear feet of main ductwork you have for the current project if the duct sizes and fitting quantity are similar.
Then you would add any of the labor corrections factors that are applicable for the current project. For example let’s say you have 200 linear feet of main ductwork. You would take the 200 feet and divide it by the historical labor feedback of 25 LF/MD which would equal 8 man days or 64 hours (200 200 LF/ (25LF/MD) = 8 Man Days or 64 Hours.
To this you would adjust for any factors effecting labor. (See course section on “Factors Affecting Field Labor.”) If you receive your ductwork from the fabrication shop KD (knocked down – unassembled), then you will have to add the time it takes to assemble the ductwork on site, which is separate from the time it takes to install the ductwork.
Additionally, if you had 3,000 feet of ductwork and fittings, and your benchmark labor database determined that it would take 800 hours to install this ductwork & fittings, this would equate to 30 LF/MD (30 linear feet per man day)
LF/HR = 3,000 Ft / 800 Hours = 3.75 LF/HR (Linear feet per hour)
To get to linear feet per man day, just multiple by 8 hours in a day.
LF/MD = (3,000 Ft / 800 hours) x 8 Hours/Day = 30 LF/MD
3.75 LF/HR = 30 LF/MD (These two represent the same labor productivity factor)
Pounds per Hour (LBS/HR)
This method is available in the SMACNA labor database as an option for labor analysis. Differing productivity values (Lbs/Hr) are used for different size and gauges of ductwork. As ducts get larger or their gauges get heavier, the duct and fittings increase in weight (pounds).
Example: if you had a 10 feet of 12” x 12” duct at 26 ga, this would equal
STEP-1 Remember that stretch-out is derived by unfolding the duct from a four sided box into a flat piece of metal, so that a 12” x 12” duct unfolded would look like this;
12” + 12” + 12” + 12” = 48” or 4 feet.
STEP-2 Determine how many pounds of sheet metal you have. We have sheet metal ductwork that is 10 feet long by 4 feet wide (stretch-out), which equates to 40 FT2.
10 feet x 4 feet = 40 FT2
STEP-3 Convert the 40 FT2 into pounds by using the conversions value for 26 gauge (0.906 LBS/FT2) galvanized sheet metal, which is.
40 FT2 x 0.906 = 36.24 LBS
STEP-4 Apply your productivity factor (LBS/HR) to the total pounds of duct at this size. Per SMACNA the productivity at this size and gauge is 24.70 LBS/HR. This would calculate out as
36.24 LBS / (24.7 LBS/HR) = 1.46 Hours
The pounds per hour labor productivity factor is the most difficult to visualize. The difficulty comes from the fact that the same five-foot piece of ductwork has different weights at the different gauges, and it’s difficult to tell how much duct weight by looking at hit. It’s easier to count how many pieces have been installed or how many linear feet. What does 300 pounds a day look like, as compared to 25 feet a man-day? It’s easier to visualize the quantity of feet or pieces.
How does the Foreman determine at the end of the day how many pounds the crew has installed? We strongly recommend that you don’t use this method, but choose one of the other labor productivity measuring factors.
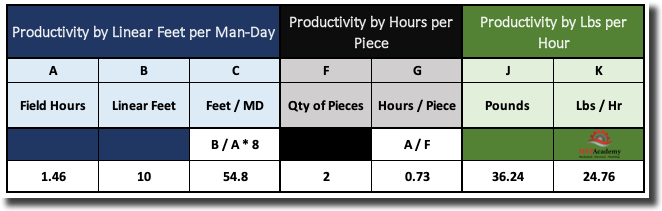
Hours per Piece (HRS/PC)
This is the second method available in the SMACNA labor database as an option for field labor analysis. Differing productivity values (HRS/PC) are used for different stretch-out sizes (perimeter). Using the same 10 foot 12” x 12” duct from above, and assuming that we are using 5 foot joint lengths, would mean that we have two (2) 5-foot sections of duct. Using the SMACNA table for low pressure galvanized straight duct with a 4 foot stretch-out and the 26 ga column, we get 0.8611 HRS/PC.
2 pieces x 0.8611 HRS/PC = 1.72 Hours
Using the same 12’ x 12” section of ductwork we can see that depending on which units of labor you use, you derive at different totals. For the LBS/HR unit labor, you get 1.46 hours, while the HRS/PC method gives you 1.72 hours based on the SMACNA database.
Once you decide on which units of labor you will use, then you should stick with it, so that you can develop a sense of familiarity.
Some prefer to use the hours per piece as a means of measuring their labor productivity in the field. This is somewhat similar to the feet per man-day in that if you know the length of each piece of duct
Practice Calculations
Calculate the LF/MD using the following information: (Answers below at end of this course)
Let’s assume your estimating software or manual takeoff has provided you with the following data;
- Rectangular Duct = 1,200 feet and 320 hours. (What is the linear feet per man-day?)
- Round Duct = 1,800 feet and 240 hours. (What is the linear feet per man-day?)
- Adjust the labor productivity to 25 LF/MD for question #1. What are the new hours?
- Adjust the labor productivity to 50 LF/MD for question #2. What are the new hours?
Military Project Labor Productivity
This chart is derived from the U.S. Military and shows what they assume it takes to put in rectangular and round sheet metal ducts based on their standard project assumptions. You should establish something similar for your company based on labor feedback from a sample of various project types. This will help you establish your standard benchmark for labor by which all future project labor would be adjusted from, such as SMACNA developed for its membership.
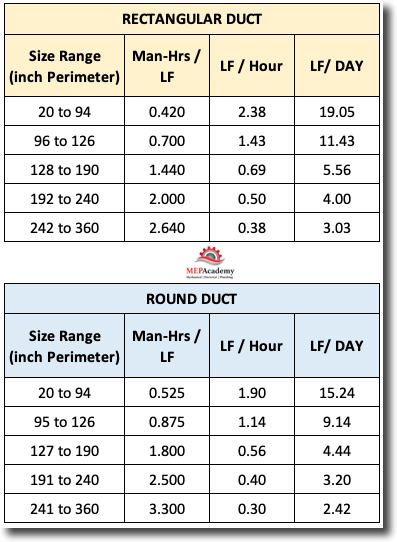
U.S. Military Sheet Metal Labor Productivity Values
Which Labor Unit Method is Best?
We prefer the LF/MD or LF/HR method of labor productivity analysis because it’s visually represented better than the others. For example, if you were to visit a jobsite to review the ductwork that has been installed, and you’re looking at a section of ductwork hanging in the buildings first floor ceiling, could you tell how many pounds of metal it is? This would require you to do some mental gymnastics, or some quick calculation as to what gauge and size the duct was in order to calculate the weight, and then divide by the productivity factor.
Productivity factors using weight in our opinion is not a good labor unit for visually inclined estimators and project managers. There must be a reason why the military uses LF/MD & LF/HR, and that is, it represents an easier way to visualize what has been installed, and for setting a benchmark for field productivity performance.
Proper Takeoff Techniques
Labor productivity factors will vary based on job site conditions as discussed above, but with everything being equal, productivity will also differ based on duct size. There is no way for a crew to install a 64” x 36” section of duct at the same productivity as a section of 12” x 12” duct. So, for this reason your adjustment factors need to be broken down as shown in the military labor unit schedule.
Benchmarking Labor Productivity Performance
When the project is under construction and ductwork begins to get installed, the project management team should begin measuring weekly what was installed and the amount of hours expended for the portion of the project related to the Sheetmetal ductwork. This will let them know if they are hitting their estimated productivity goals.
This is done by taking a fresh new set of drawings out to the jobsite for benchmarking the performance that occurs each week. Each week the ductwork on the drawings that has been installed gets colored on the drawings, documenting the progress of the project. Back at the office, the ductwork that was colored in for that week gets taken off to determine how many linear feet of ductwork was installed compared to how many hours were charged for installing the ductwork that week.
If the sheet metal crew had installed 900 feet of ductwork and they used a six person crew for a week, then the actual productivity would be as follows;
6 Crew Members x 40 Hours/Wk = 240 Hours spent
900 Feet / 240 Hrs = 3.75 LF/HR or 30 LF/MD
Correction/Adjustment Factors
The correction factors shown below are used to adjust a base unit of labor that is considered normal conditions. The correction factors then would adjust this normal condition base unit for any conditions out of the norm. If you review MCA and SMACNA labor units their method is similarly based on a standard unit of measure for which unusual conditions are adjusted. Labor productivity will vary by building type and projects, and may require more or less than the benchmark database labor.
These adjustment factors are just suggestion, and are not hard percentages that you should rely on. All labor adjustments should be something that is derived from experience and historical data that your company tracks. This applies to all the adjustment factors shown in this course.
Height of Installed Ductwork: Anytime your ductwork is hung above 10 to 13 feet you will need to adjust for the increased height. If the field labor can’t work off ladders then you will need some type of scaffold or scissor lift. Add 2% to 10% for ducts hung 11’ to 15’: add 10% to 20% for ducts hung from 16’ to 20’, and so on:
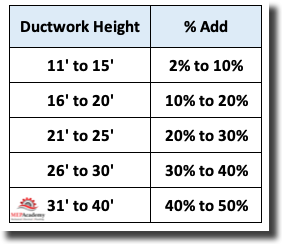
Quantity of Floors: As mentioned above the quantity of floors will have an impact on your labor when the quantity of floors exceeds three. This is the additional time it takes to reach higher and higher floors in the building.
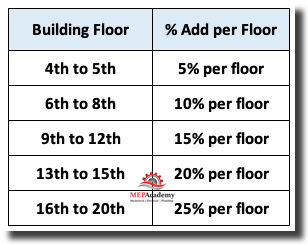
Weather Conditions
We all know what it’s like to work in excessively hot or cold weather. Workers just don’t perform at the same productivity levels as they do under normal weather conditions. You can get more done in a nice controlled environment than if you had to work on a cold concrete floor on the 10 floor of a new high-rise that has no walls installed yet, and the cold wind is blowing through the building.
If the project will be built during extreme weather conditions, than you should adjust for a loss of productivity due to the weather. The question is what would the weather conditions be during the duration of the project?
Extremes of either hot or cold weather will result in a loss of labor productivity. Humans don’t function as well when the temperature of the ambient air is outside their comfort zone. This goes for working in areas such as hot boiler rooms or equipment rooms where the temperature is outside the normal range for human comfort.
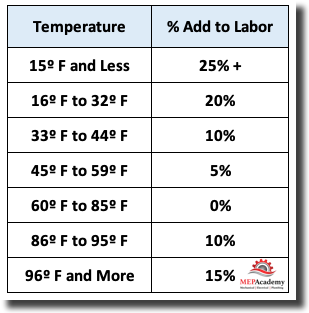
Field Labor Feedback
If you have been in business for any period of time you have established some historical data on the field time required to install ductwork, equipment and accessories. From this historical data, you can project what kind of productivity you should get for the current, similar job. If the jobs are not similar, then you must adjust the productivity up or down depending on the current projects relative ease or difficulty compared to your historical project.
There is no better measure of productivity than your own historical data, but each job will still be unique and should be carefully scrutinized for those areas where productivity could be affected.
Answers to Practice Calculations
- 30 LF/MD (1,200 LF/320 hours) x 8 hrs/day)
- 60 LF/MD = (1,800 LF/240 hours) x 8 hrs/day
- 384 Hours (1,200 LF/ 25LF/MD) x 8
- 288 Hours (1,800 LF/ 50LF/MD) x 8
Sheet Metal Field Installation Course (Free)
- Chapter #1- Rectangular Duct and Fittings
- Chapter #2 – Round Ductwork and Fittings
- Chapter #3 – Sheet Metal Duct Hangers
- Chapter #4 – Sheet Metal Field Labor Productivity
- Chapter #5 – Labor Crew Sizes
- Chapter #6 – Sheet MetalDuct Sealer
- Chapter #7 – Sheet Metal Details and Specialties
- Chapter #8 – Grease Exhaust
- Chapter #9 – Air Distribution
- Chapter #10 – Rental Equipment
- Chapter #11 – Conditions Affecting Field Labor
- Chapter #12 – HVAC Equipment Labor