In this article we explain the fundamental concepts of static pressure (Sp), velocity pressure (Vp), and total pressure (Tp) in the realm of HVAC systems. Understanding these pressure components is essential for designing, maintaining, and optimizing air conditioning ducts. In this article, we will explore the definitions of static, velocity, and total pressure, their significance in HVAC engineering, and practical insights on the instrument commonly used to measure them.Â
If you prefer to watch the video of this presentation, then scroll to the bottom.
Atmospheric Pressure
Atmospheric pressure is the force exerted by the weight of the air above a specific point on the Earth’s surface. It is the pressure exerted by the Earth’s atmosphere on objects within it. At sea level atmospheric pressure is approximately 14.7 psia (pounds per square inch absolute) or 1,013 millibars.
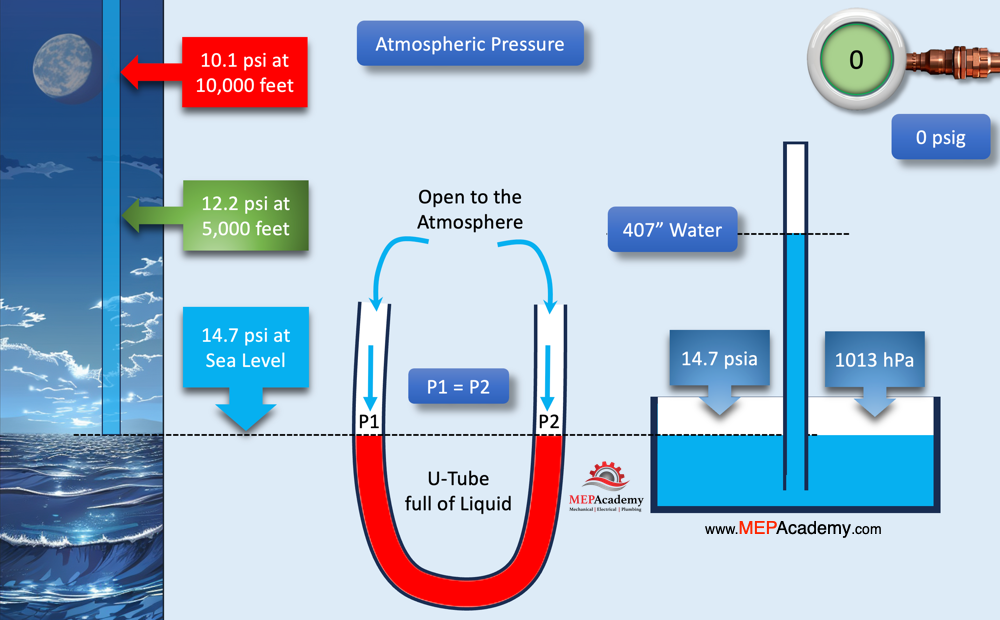
Atmospheric pressure decreases with altitude. HVAC systems in high-altitude locations may require adjustments to account for lower atmospheric pressure, affecting factors such as air density and combustion processes.
Using a U-tube manometer with both ends open to the atmosphere, the liquid level on both sides of the tube rest at the same height. This is because both ends of the tube are open and exposed to the same atmospheric pressure.Â
Static Pressure
SP is the pressure exerted by the air in all directions within the ductwork when it is not in motion. It is a measure of the potential energy of the air as it remains static or stationary within the system.Â
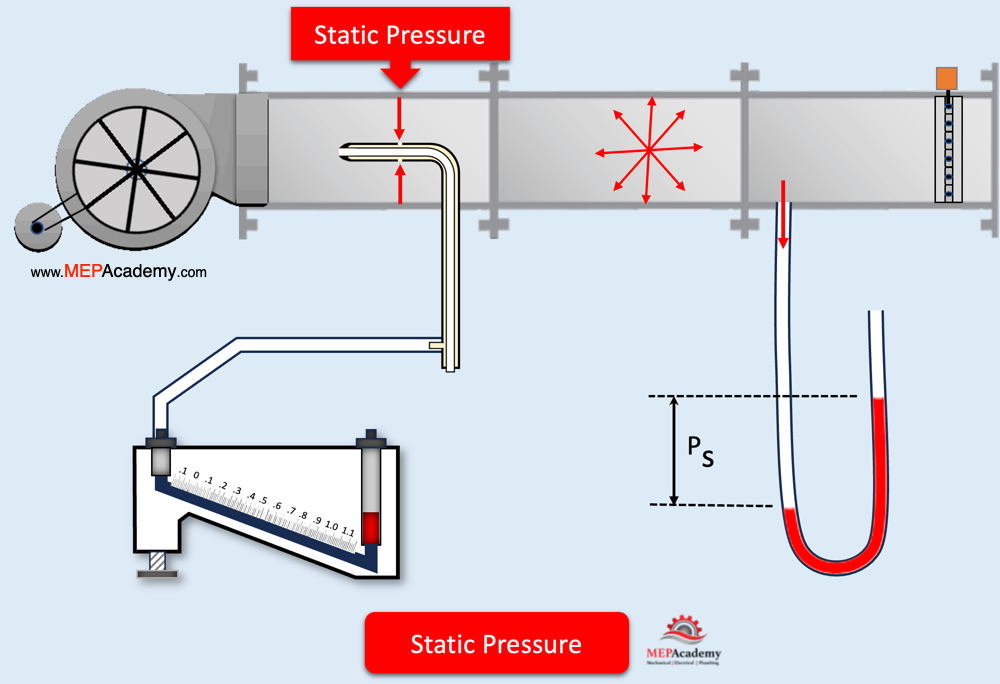
Static pressure is the force exerted by the air on the walls of the ducts and other components when the air is not flowing. It is typically measured in units such as inches of water column (inWC) or pascals (Pa) using an inclined manometer as shown in image.
Air encounters resistance as it moves through ducts, filters, coils, and other components. This resistance generates static pressure. When choosing a fan for an HVAC system, consideration must be given to the static pressure the fan must overcome to deliver the required air to the space.
The layout and design of the ductwork, including bends, transitions, and fittings, can contribute to an increase in pressure.
High static pressure can lead to increased energy consumption, as the system must work harder to overcome resistance.
(Sp) affects the airflow within the ducts. Excessive pressure may result in reduced airflow, impacting the system’s ability to deliver conditioned air to the desired spaces.
Velocity Pressure
The Velocity pressure is the pressure component associated with the movement of air within a duct.Â
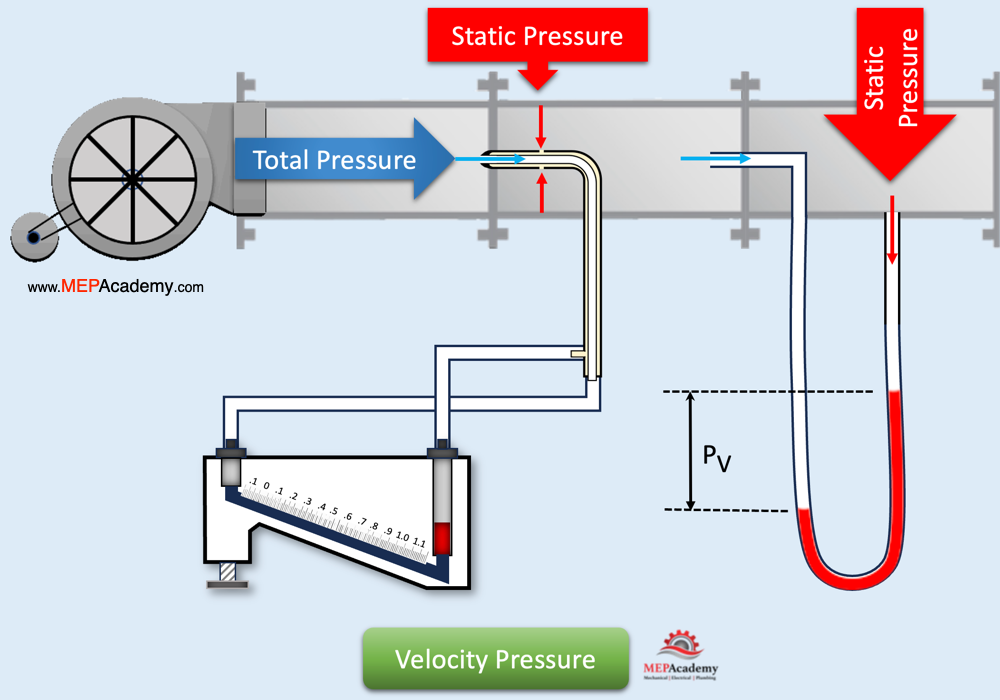
Consider a scenario where a fan is propelling air through a duct system; during this process, two distinct pressures come into play – velocity pressure and static pressure. The combination of these pressures is termed total pressure. Velocity pressure, arising from the movement of air, can be quantified by determining the variance between total pressure and static pressure, with pressure units denoted in inches of water (W.G.) or pascals (Pa).
Direct measurement of velocity pressure is not done; instead, the most straightforward method to ascertain the airflow velocity is by assessing the velocity pressure within the duct using a pitot tube assembly linked to a differential-P sensor, comprising both a static and total pressure probe.
The pitot tube can be inserted into the airflow to measure both static and dynamic pressures. The dynamic pressure measured by the pitot tube represents the velocity pressure.
Total Pressure
A total pressure probe, positioned in line with the airflow, detects both the duct’s velocity pressure and static pressure, resulting in the total pressure. Meanwhile, a static pressure probe, oriented perpendicular to the airflow, exclusively measures static pressure. The disparity between the total pressure reading and the static pressure reading represents the velocity pressure.
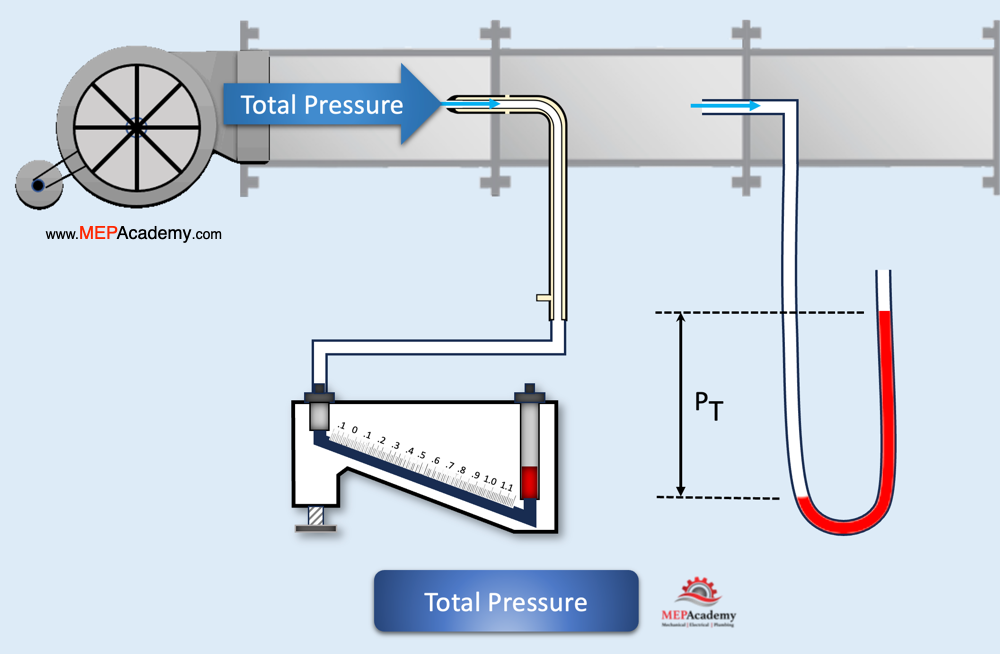
Devices used to Measure Pressure
In our example we used an inclined manometer, but there are many other ways to measure pressure, velocity and air flow. Manometers or pressure gauges are commonly used to measure static pressure within the ductwork.
Inclined Manometer
A manometer is a straightforward and widely used instrument for measuring pressure. There are different types of manometers, including inclined, vertical, and digital versions.
Inclined ManometerTo measure static pressure using a manometer, connect the instrument to pressure taps on the duct—one at the high-pressure point and one at the low-pressure point. The difference in fluid levels in the manometer provides the static pressure reading.
ManometerDigital Pressure Gauge
Digital pressure gauges are modern instruments that provide accurate and quick static pressure measurements. These gauges typically have a display screen that shows the pressure readings directly.
Connect the gauge to the pressure taps on the duct, and it will display the static pressure.
Pitot Tube and Differential Pressure Sensor
A pitot tube can be used in conjunction with a differential pressure sensor to measure pressure. The pitot tube is inserted into the duct, and the differential pressure sensor measures the pressure differences.
Pitot TubeThe static pressure is then determined by subtracting the velocity pressure from the total pressure measured by the pitot tube.
Capture Hoods
Capture hoods are devices designed to measure both air volume and static pressure at diffuser and grille locations. They consist of a hood that covers the diffuser or grille, and a connected manometer or pressure gauge provides the static pressure reading.
Magnehelic Gauge
A Magnehelic gauge is a type of pressure gauge commonly used to measure air and gas pressures. It is easy to use and can be installed directly on the duct. The gauge displays the pressure difference between the duct and the ambient air.
Magnehelic GaugeBalometer
A balometer is a specialized instrument used for measuring air volume and velocity, but it often includes a pressure measurement component. It is particularly useful for assessing airflow at diffusers and grilles.
Airflow HoodWhen measuring static pressure, it’s important to follow these general steps:
– Identify suitable pressure tap locations on the duct.
– Ensure proper sealing of the instrument to prevent air leaks.
– Take measurements at various points to assess uniformity and identify potential issues.
– Compare readings with design specifications to evaluate system performance.
Always follow manufacturer guidelines and safety precautions when using any measuring instrument in an HVAC system. Regular static pressure measurements help HVAC professionals maintain and optimize system performance.
Air Velocity
Air velocity is the speed at which air moves through a duct or HVAC system, typically measured in feet per minute (fpm) or meters per second (m/s). Controlling air velocity is essential for maintaining comfort and efficiency. Low velocity may lead to inadequate air distribution, while excessively high velocity can result in noise, pressure drops, and increased energy consumption. Engineers need to optimize air velocity to achieve the desired airflow without causing discomfort or system inefficiencies.
In summary, understanding and carefully managing air pressure and velocity are critical for designing HVAC systems that deliver optimal performance, comfort, and energy efficiency in the construction projects you work on, such as commercial buildings, hospitals, hotels, and other facilities.