Domestic Hot Water Recirculation System. A lot of water gets wasted waiting for the hot water to arrive at a sink, bathtub, shower or other plumbing fixture. We’ll show you how residential and commercial domestic hot water recirculation systems work to save water, energy, time and money.
If you prefer to watch the video version of this presentation, then scroll to the bottom or click on this link. Domestic Hot Water Recirculation System
We’ll start by showing you three basic residential systems. Domestic hot water recirculation systems are designed to provide instant hot water to various fixtures and appliances throughout a home, such as faucets, showers, and washing machines, by circulating hot water continuously through the pipes, so as to avoid waiting for the water to heat up.
System #1 is the Traditional Residential System with a Dedicated Return Line.
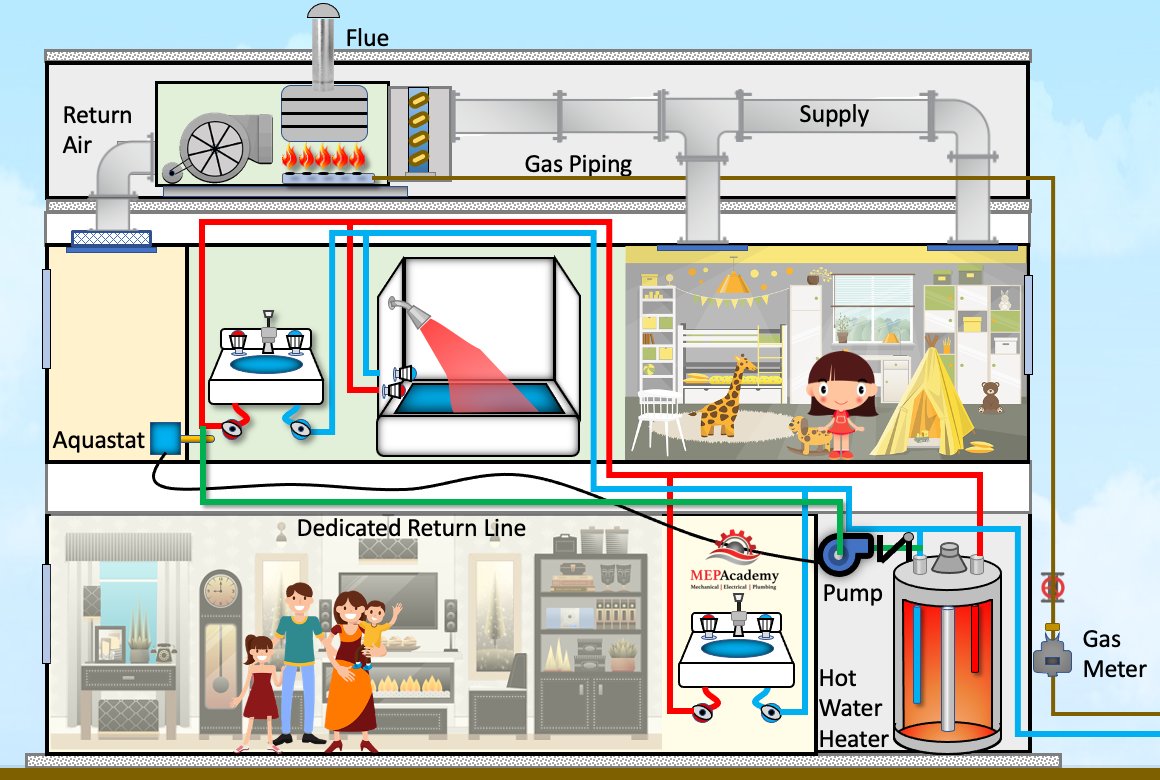
- A dedicated return line is installed that connects the furthest hot water fixture in the home back to the water heater. This line allows hot water to circulate continuously back to the water heater in a continuous loop.
- A recirculation pump is installed on the hot water return line, typically near the water heater. The pump is designed to move hot water from the farthest fixture through the dedicated return line back to the water heater.
- A check valve is installed on the return line to prevent hot water from flowing back into the return piping.
- A timer or thermostat is installed to control when the recirculation pump operates. To ensure that the recirculation system operates efficiently, a temperature sensor or timer is installed near the pump. The sensor or timer controls the pump to circulate hot water only when needed.
- When hot water is needed at a fixture, the pump is activated and hot water is quickly circulated through the pipes, providing hot water almost instantaneously.
- The return line ensures that hot water is constantly recirculated, so there is always hot water available when needed.
If the home wasn’t pre-piped with a dedicated return line, then the following two options are available to avoid an evasive renovation project.
Under the Sink Residential System #2
A bypass valve is installed at the furthest fixture to allow the hot water line to circulate back to the water heater using the cold water piping. The Bypass valve stays closed while the hot water temperature is warm.
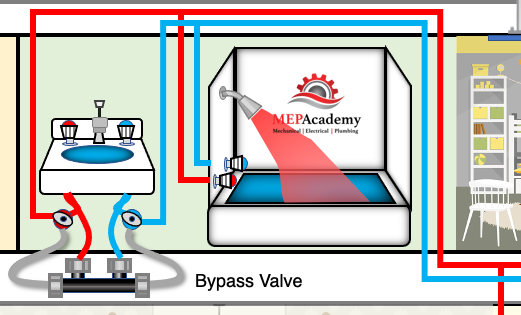
A pump is installed on the hot water line at the water heater. When the temperature of the water at the furthest plumbing fixture cools down the pump will turn on and circulate hot water from the water heater through the bypass valve and into the cold water line until the temperature is warm enough. The pump is turned on by a timer that is set by the user to come on when the residents normally need hot water. The system can be easily installed within a couple of hours.
Under the Sink Residential System #3
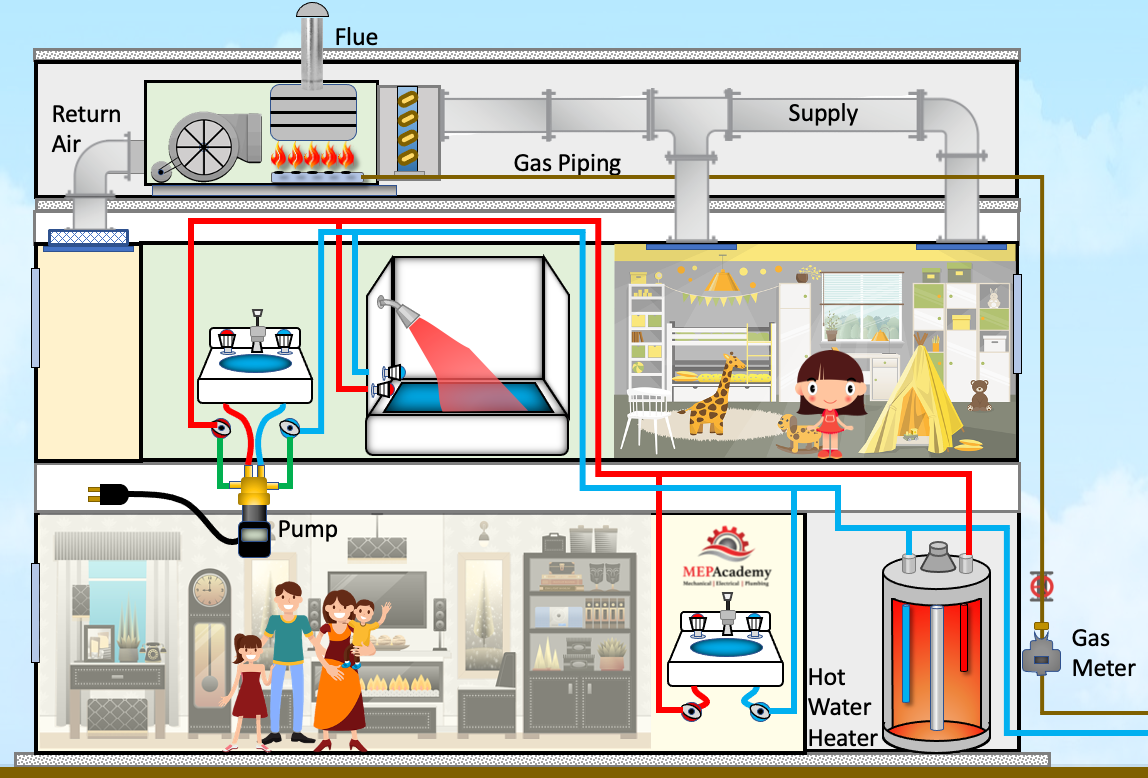
There is a simple on demand hot water recirculation system that can be added to the furthest fixture, in our case a pump is added to the sink on the second floor of this home. The piping is reconfigured so that the water is fed through the recirculation pump housing manifold. The manifold is then connected to the sink. There is no hot water recirculation line, instead the pump has a temperature sensor that will shut off the pump when the temperature reaches it setpoint of 110F (43C), or whatever the customer sets it at. A little of the hot water will be sent into the cold water line until the temperature sensor shuts off the pump.
There are options on how to control the pump. By installing an Aquastat or temperature sensor the pump can turn on when the hot water temperature drops to 85F (29C) and keep running until the stat reads 105 F (40 C), at which point it shuts off.
Another option is that there could be a timer set to bring the pump on at a certain time each day, lets say 6:00 am, a half hour before the family gets up. This would allow for the hot water to be ready for use at any fixture.
Another option is a switch that is manually turned on or remotely if using a wireless App. With this option the pump could be set to turn off and on every 15 minutes to maintain hot water at the fixtures.
This avoids wasting time waiting for hot water, saves money and stops wasting water.
Commercial Hot Water Recirculation System
When selecting a commercial hot water recirculation system, it is essential to consider factors such as the building’s size, water usage patterns, and energy efficiency goals.
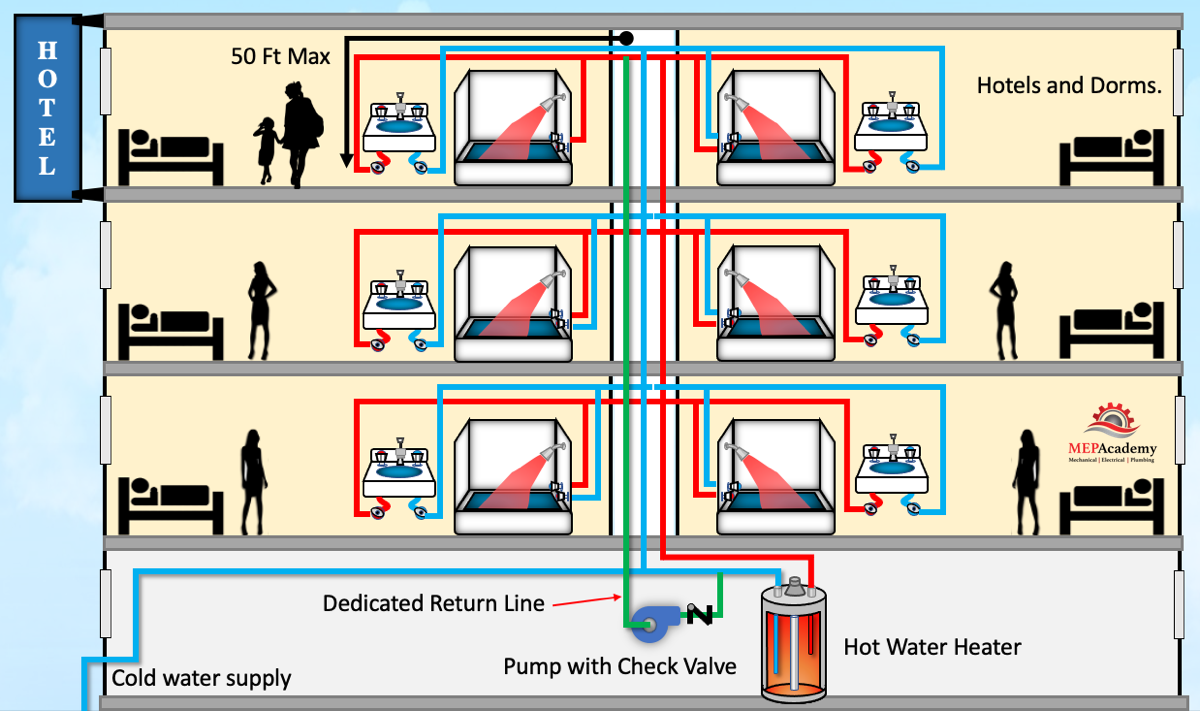
Here is a simple explanation using a small hotel with one main riser.
A hot water recirculation pump will be installed along with a dedicated return line that is connected to the hot water piping at a point that provides a maximum of 50 feet in piping distance to the furthest fixture requiring hot water. The International Plumbing Code IPC, section 607.2 states that the distance from the source of hot water to the fixture shall not exceed 50 feet.
Then a check valve along with the discharge piping is connected to the cold water piping feeding the water heater. This is the basic layout. Of course there are many factors to consider when designing a commercial system so consulting with a qualified mechanical engineer can help ensure that the system selected is appropriate for the building’s specific needs and requirements.
When hot water is turned on at a fixture or appliance, the water in the dedicated return line is pushed back to the water heater. The pump then circulates hot water from the water heater through the dedicated return line, and the hot water is quickly available at the fixture or appliance.
Overall, a domestic hot water recirculation system can save water and energy by reducing the amount of time it takes for hot water to reach fixtures and appliances, and by minimizing the amount of water that is wasted while waiting for hot water to arrive.
Some recirculation systems use a thermostatic valve at each fixture, which automatically turns on the pump when the water temperature drops below a certain level. This can save energy by reducing the amount of time the pump needs to run.
Overall, a domestic hot water recirculation system can provide convenience and save water by reducing the amount of time it takes to get hot water at a faucet or shower.
Various Recirculation System Types
There are various types of commercial hot water recirculation systems available in the market, including:
- Pump-based systems: In this type of system, a pump is installed in the hot water line, which circulates hot water continuously through the pipe. A return line is also installed, which sends the cold water back to the water heater.
- Demand recirculating systems: In this type of system, a pump is activated only when there is demand for hot water at a specific faucet or fixture. This system typically uses a thermostatic valve to regulate the water temperature and a timer to control the pump.
- Gravity-fed recirculating systems: This system uses the natural convection of hot water to circulate it throughout the building. The system is designed so that the hot water rises to the upper floors of the building and then circulates back down through the return line.
Commercial hot water recirculation systems can save significant amounts of water and energy by reducing the time it takes for hot water to reach the tap. They are commonly used in hotels, hospitals, schools, and other commercial buildings where hot water demand is high.
Benefits of Hot Water Recirculation Systems
There are several benefits to using a hot water recirculation system in a commercial or residential building, including:
- Improved energy efficiency: With a hot water recirculation system, hot water is constantly flowing through the pipes, reducing the amount of time it takes for hot water to reach its destination. This can result in significant energy savings, as less energy is required to heat the water.
- Increased convenience: With a recirculation system in place, hot water is always available when needed, which can be a significant convenience for businesses that rely on hot water for their operations.
- Reduced water waste: By reducing the amount of time it takes for hot water to reach its destination, a recirculation system can also reduce water waste, as less water is wasted while waiting for hot water to arrive.
- Improved hygiene: With hot water readily available at any tap or fixture, businesses can ensure that their employees and customers have access to hot water for hand washing and other hygiene-related activities.
Domestic hot water recirculation systems work by continuously circulating hot water from the water heater through a dedicated loop of pipes to the fixtures that require hot water, such as faucets and showers. This helps to reduce the amount of time it takes for hot water to reach these fixtures, which can help conserve water and energy.
Overall, hot water recirculation systems can provide a convenient and efficient way to deliver hot water to fixtures, while also reducing water waste and improving energy efficiency.
There are several types of hot water recirculation systems available for commercial use, including traditional and demand-controlled systems. Traditional systems continuously circulate hot water through the pipes, while demand-controlled systems only operate when hot water is needed. The choice of system will depend on the specific needs and requirements of the business in question.
ASHRAE 90.1-2022
7.4.4.2 Temperature Maintenance Controls
Systems designed to maintain usage temperatures in hot-water pipes, such as recirculating hot-water systems or heat trace, shall be equipped with automatic time switches or other controls that can be set to switch off the usage temperature maintenance system during extended periods when hot water is not required.
7.4.4.3 Outlet Temperature Controls
Temperature controlling means shall be provided to limit the maximum temperature of water delivered from lavatory faucets in public facility restrooms to 110°F.
7.4.4.4 Circulating Pump Controls
When used to maintain storage tank water temperature, recirculating pumps shall be equipped with controls limiting operation to a period from the start of the heating cycle to a maximum of five minutes after the end of the heating cycle.
Timer Control
The pump is turned on and off according to a programmed schedule.
If schedule is set to have the pump off when hot water is requested, then water will be wasted.
Temperature Control
With the use of a temperature-controlled system, the pump will turn on and off to maintain the temperature setpoint on the return water piping, usually 120F.
This method keeps a minimum return temperature.
Temperature Modulation Control
This is a mixture of temperature control and scheduled control. The temperature of the domestic hot water supply is changed throughout the day based on the occupancy usage patterns. This could be high demand in the early morning for multifamily residential buildings where occupants are waking up and preparing for their daily activities or going to work. This method attempts to match occupancy behavior to a schedule for setting hot water supply temperatures.
Demand Control
Hot water demand for this method of control uses real-time user input and return water temperature. The pump will run if the controls detect water flow, and the temperature of the return water has dropped to a certain minimum setpoint such as 100F.
Demand control and temperature modulation work the best when combined into one system approach for energy and water savings
Summary
Hot water recirculation systems are typically installed to improve energy efficiency, reduce water waste, and enhance user convenience. By circulating hot water through the building’s supply lines, these systems can minimize the amount of water that goes to waste while waiting for hot water to arrive at the faucet or showerhead.
When designing a domestic hot water system use a compact layout where the distribution to any fixture requiring hot water is a short distance from the source. Install a recirculation pipe with short branches to each fixture requiring hot water.