In this article we’ll cover the workings of a typical household plumbing system, which is also applicable to some commercial buildings. Practically everything we do relies on plumbing, whether it’s washing your car, clothes, or dishes, and/or brushing your teeth before bedtime. The backbone of these activities is your home’s plumbing system, consisting of four key elements: waste drains, waste vents, potable water, and rainwater management.
Let’s explore each system individually and understand their functions.
If you prefer to watch the video of this presentation, then scroll to the bottom.
Waste and Vent Sewer System
In most homes the sewer waste system is installed using ABS, PVC, or cast-iron drainpipes and vents. These pipes interconnect with fixtures like toilets, sinks, bathtubs, and showers. When a fixture is used, waste travels through these drainpipes, which are required to be sloped to keep things moving. The waste will ultimately reach the municipalities main drain beneath the street.
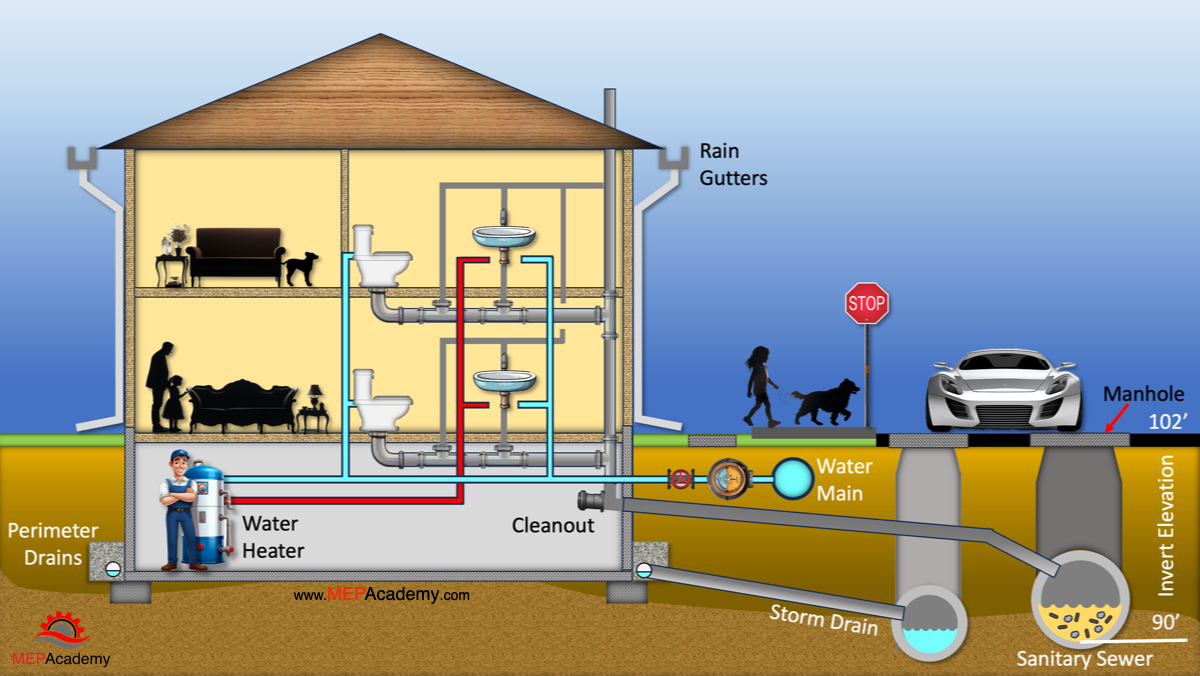
Periodically, you’ll come across clean-outs, like this one. These provide access to the inside of the pipes in case of a blockage and are required by your local code. In the United States, many homes have these cleanouts located outside for easier access by plumbers.
Fixture Units
Plumbing pipe sizes are based on what is called “Fixture Units”. Each type of fixture is given a fixture unit value that corresponds to a pipe size. The code contains a chart listing these values. See our other video on “How to Size Plumbing Water Pipes using Fixtures Units” as the process is similar for waste pipes. Main stacks range from three to four inches, depending on code requirements and municipal regulations.
However, some homes lack municipal wastewater treatment services. In such cases, waste disposal is straightforward. The main drainpipe, which would typically lead to the municipal sewers, connects to a septic tank instead, often made of concrete or polyethylene. This tank separates solids from liquids before directing them to a leach field or drain field in the ground for natural solid filtration. Periodic pumping by a vacuum truck is necessary to ensure proper functionality.
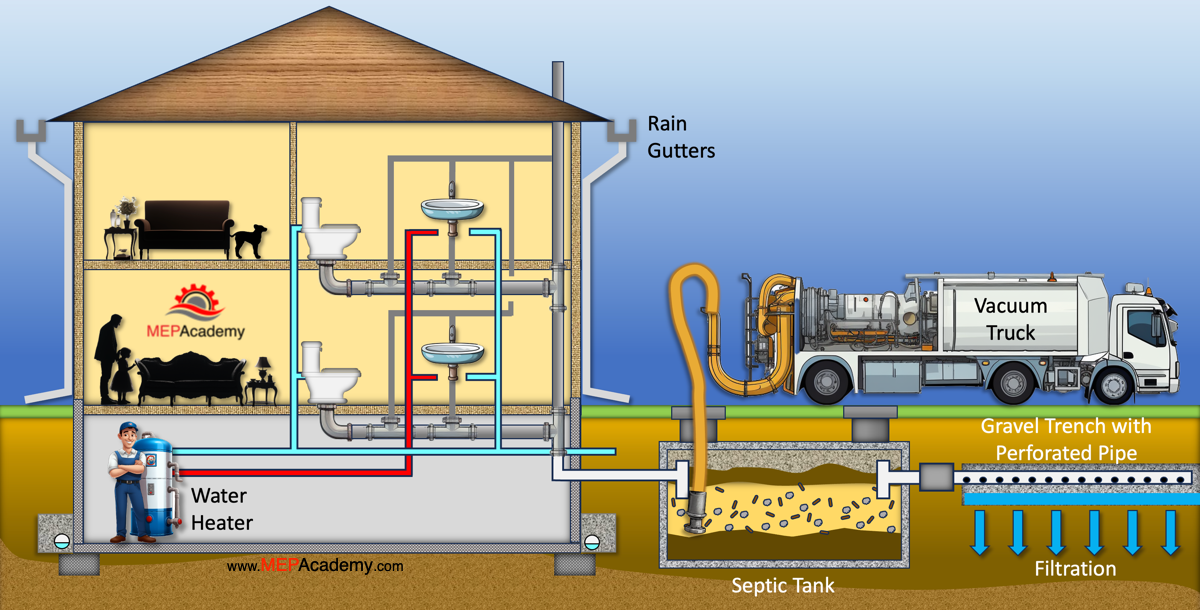
Now, let’s delve into venting. For the effective operation of these fixtures and drains, a well-designed venting system is essential. When a toilet is flushed, for instance, the water’s downstream flow induces negative pressure. Vents play a crucial role in equalizing this pressure change, preventing issues such as gurgling and the siphoning out of water in pee traps. This prevention is vital to avoid the infiltration of sewer gases into your home.
These vents draw in air from the roof, and it’s imperative to keep them clear of bird nests and debris, or complications are guaranteed.
Potable Drinking Water
Regarding potable water, it originates from the municipal water main buried in the street, like other services, and typically maintains a pressure range of 40 to 80 PSI. Every residence connected to this city’s water supply must feature an outdoor water meter and shut-off valve, like the one shown. This allows the city to determine how much water is consumed and to shut off services in cases of emergency or if service is discontinued. The incoming copper line is usually 3/4 to 1 inch in diameter, depending on the size of the home. The pipe enters the basement through the concrete slab, or through the first floor. This usually leads to another shut-off valve that is more accessible to the homeowner.
In the basement, first floor, or garage, we encounter the hot water heater and storage tank. Other designs may use tankless water heaters. Whether electric or gas-fed, this tank receives cold water, heating it before distributing it throughout the house, courtesy of the city’s water pressure. While some homes still use copper lines, new construction projects often utilize PEX piping due to its reliability and rapid installation. Some older homes may have galvanized pipe and fittings that tend to become clogged over time. We will suggest re-piping if you have old, galvanized pipes.
Private Well Water
How does one obtain water in the absence of municipal services? In rural regions, individuals rely on wells. A well is essentially a vertically drilled hole deep in the ground to tap into groundwater, which is pumped up. The pumped water undergoes a series of processes and filtration to ensure its drinkability.
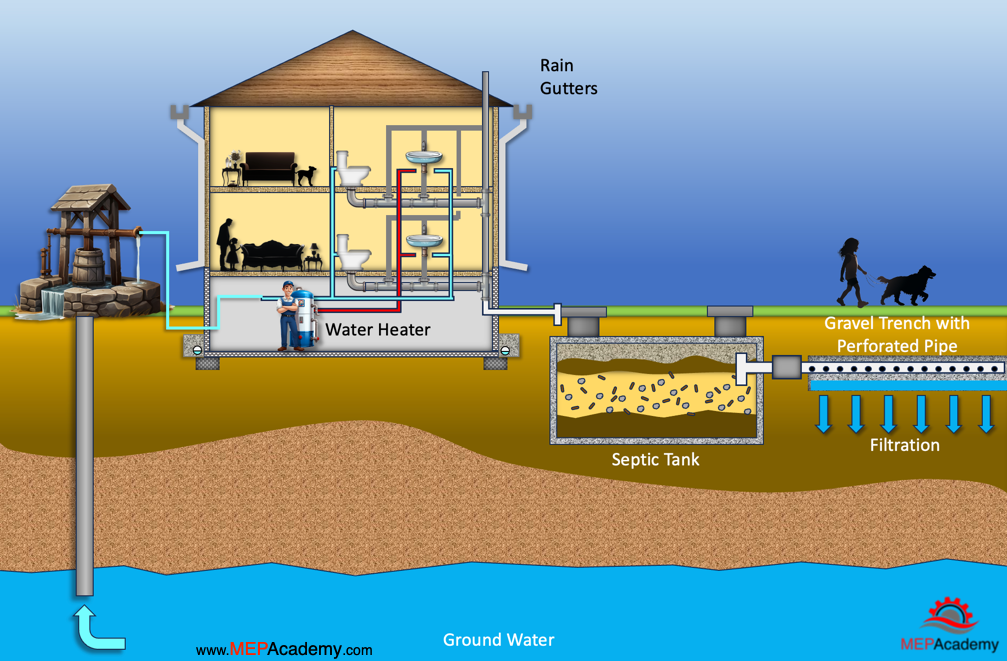
Public water systems comprise 90% of all water supplied. In areas without municipal services, wells are common. About 13 million US households get their water from private wells.
The water you receive from your faucet might originate from distant sources spanning hundreds of miles. Public water systems commonly derive their supply from either surface water, like lakes and rivers, or from groundwater. The drinking water can be stored behind a dam, or in tanks before being pumped to your home.
Rainwater Storm Systems
The final aspect is rainwater management. Historically, rainwater and sewage were combined, meaning rainwater and household waste flowed into the same sewer. However, modern practices have separated them to streamline water management. So, when it rains, the question arises: where does all this water go?
Rain falling on the house’s roof travels into the gutters. The primary role of gutters is to redirect water away from the house, preventing water infiltration. There may also be pool deck and area drain’s that drain to the streets storm drain system.
Alternatively, some people opt to collect the rainwater from the roof gutters into rainwater barrels for non-potable use, such as watering plants and flowers.
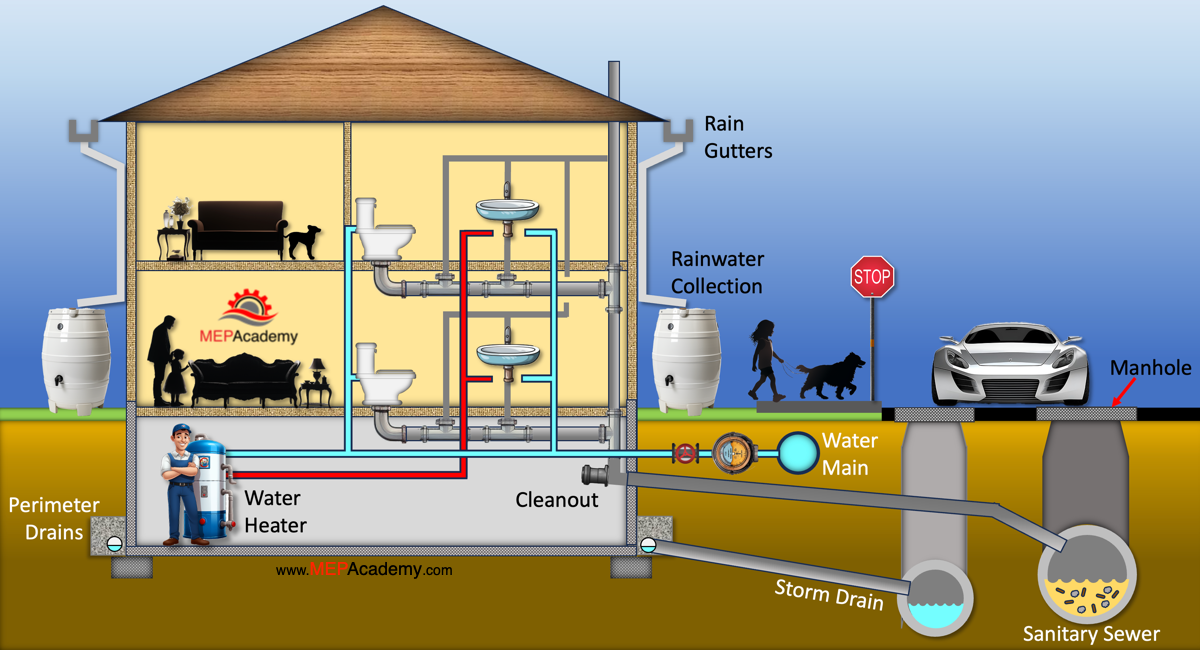
Sewer Waste Treatment
Now, where does all the waste and rainwater go once it leaves your home?
The municipal waste and storm drain mains usually follow the road. The wastewater main will eventually reach a lifting station that pumps the wastewater back up to prevent it from going too deep into the ground. This is because the system is pitched downward to keep everything moving by gravity. The longer the distance from your home, the deeper the main gets, which is referred to as its invert elevation.
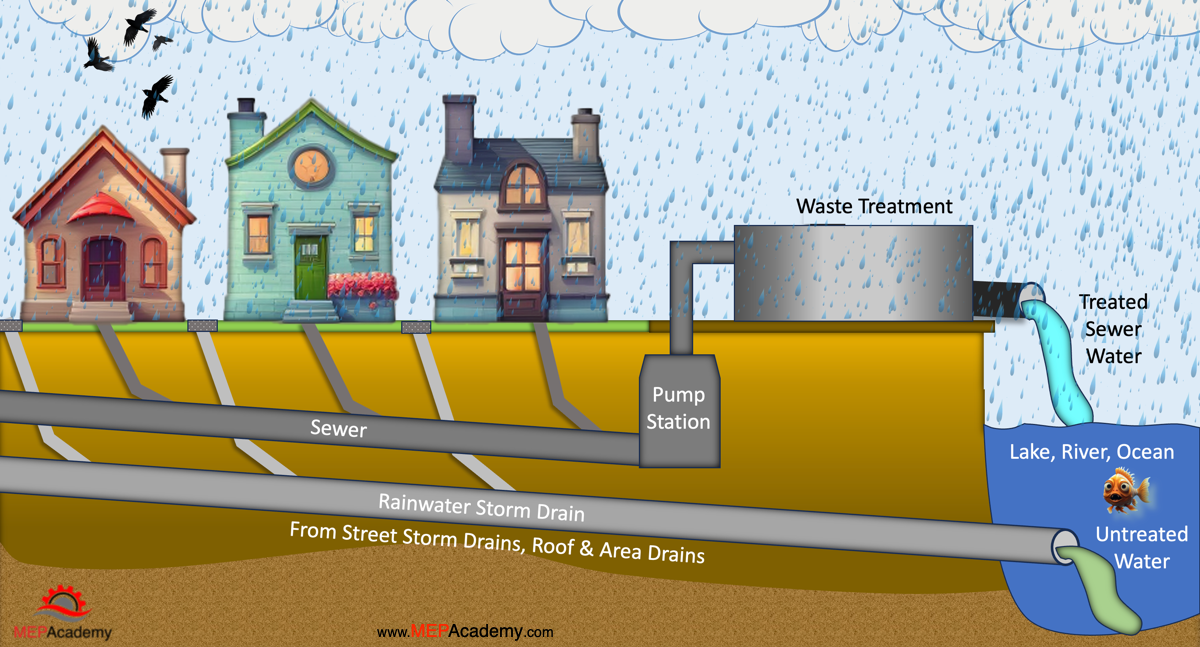
In the context of underground plumbing mains, the term “invert elevation” refers to the elevation or height of the inside bottom surface of a pipe. It is the lowest point inside the pipe where the flow of wastewater or sewage is present. The invert elevation is a crucial measurement as it helps determine the slope or gradient of the sewer line.
The wastewater is sent to a treatment plant where the nasty stuff is filtered out before being dumped into a lake, river, or ocean.
Unfiltered Rainwater Storm Drain
The Rainwater storm drain flows into a nearby river, lake, or ocean without being filtered or treated. According to the EPA, rainwater runoff picks up fertilizer, oil, pesticides, dirt, bacteria, and other pollutants as it makes its way through storm drains and ditches – untreated – to our streams, rivers, lakes, and the ocean. Polluted runoff is one of the greatest threats to clean water in the U.S. That’s why it’s important not to dump anything in the storm drain that you wouldn’t want to be swimming in the lake or ocean with, or drinking.
In essence, this is the fundamental process of how your plumbing system operates.