In this presentation we’ll learn how Chillers and Air Handling Units (AHU’s) work together in commercial buildings. We’ll discuss the basic functions of these systems and the advantages and disadvantages of air-cooled versus water-cooled chillers.
For the YouTube video Presentation of this, scroll to the bottom.
Air-Cooled and Water-Cooled Chillers
Chillers provide the source of the chilled water that feeds the cooling coil within the air handling unit and fan coils. Supply Air will blow over the chilled water coil in the AHU or FCU to provide cool air to the spaces in the building. The chilled water coil absorbs the heat from the air passes over them and takes the heat back to the chiller where it will be rejected to the outside.
The two most common types of chillers are air-cooled and water-cooled. This refers to the method by which the chiller ejects the heat from the system.
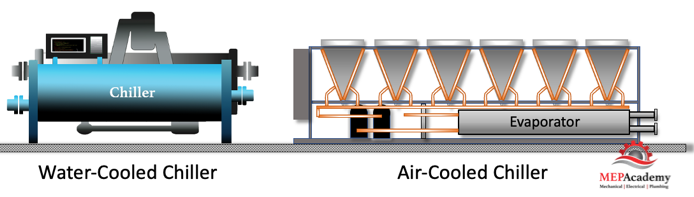
With a packaged air conditioning unit, the room air passes directly over a coil filled with refrigerant, while in a chilled water system the room air passes over a coil filled with chilled water.
Water-cooled chillers are manufactured in larger tonnages than air-cooled. Some manufactures make water-cooled to 6,000 tons (20,500 kW), and their air-cooled versions to 600 tons (1,900 kW).
Air-Cooled Chiller vs Water-Cooled Chiller
An air-cooled chiller uses fans to reject the heat outdoors, while a water-cooled chiller will require a cooling tower that sends water to the chiller to absorb the unwanted heat, and then eject that heat through the tower process.
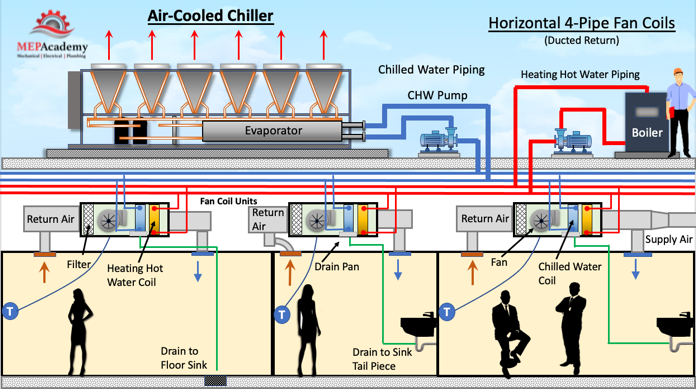
An air-cooled chiller comes as a packaged unit from the factory including the compressor, evaporator and condenser, with the option of having chilled water pumps integrated. The water-cooled chiller needs a lot more equipment including the cooling tower, water treatment, drain lines and some form of sand or centrifugal filter. This causes air-cooled chillers to have a lower installed cost, simpler installation, lower cost for maintenance due to less components and no water issues or chemicals to deal with.
The water-cooled chiller will usually be more energy efficient, due to the fact that the compressor will have to do less work because water-cooled chillers have lower condensing water temperatures and pressures. Water-cooled chiller usually have a longer equipment life because they’re mostly installed indoors, while air-cooled chillers sit outdoors exposed to the elements. Water-cooled chillers have a life expectancy of 20 to 30 years, while air-cooled chillers is around 15 to 20 years.
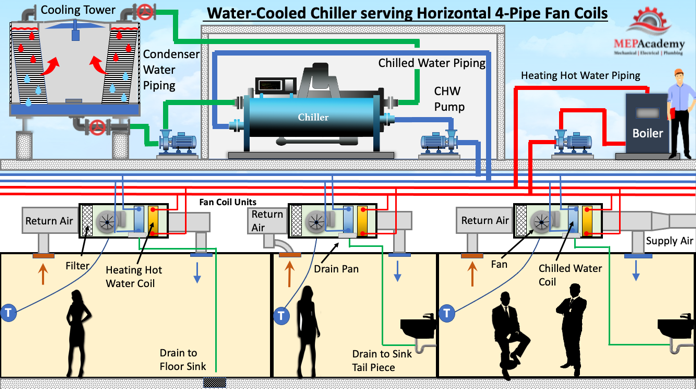
If the HVAC contractor installs an air-cooled chiller on the roof of a building with horizontal fan coils, then installs the piping and pump, the systems is complete except for electrical power and controls.
Using the same building, If the HVAC contractor were to install a Water-cooled chiller and space wasn’t available on the ground level, a penthouse might need to be built on the roof to house the chiller, while additional structural reinforcement of the roof might be required for the weight of the cooling tower full of water.
Water-cooled chillers need a cooling tower, and the tower requires makeup water and a drain. Also some form of chemical treatment will be required for the tower water to remain stable and avoid corrosive buildup.
With an air-cooled chiller you have no cooling tower. The installation is much easier, and it avoids the additional use of water and chemicals. If water is expensive and energy is cheap, than an air-cooled chiller might be the best option. If energy is expensive and water is cheap than the water-cooled chiller may provide the best solution.
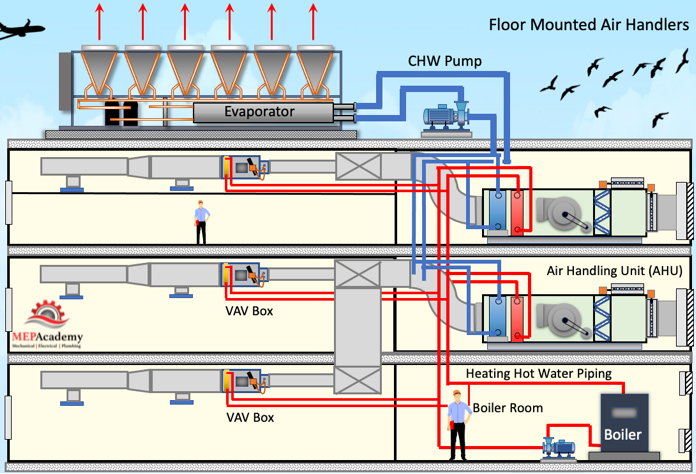
Here are chillers feeding air handling units and the difference between an air-cooled and water-cooled installation in the same building.
Using an air-cooled chiller can free up valuable space within a building that would otherwise be required for an water-cooled chiller. This additional space can be rented out, increasing the value of the building.
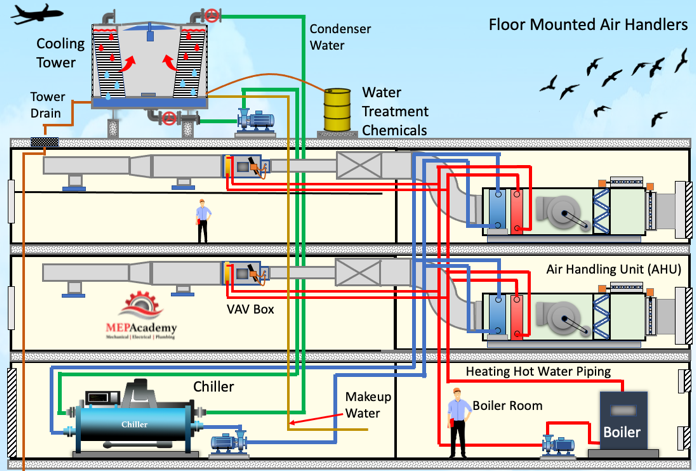
Water-cooled chillers are mostly installed indoors. This is one of the factors that leads to a longer equipment life, in the range of 20 to 30 years, as compared to an air-cooled chiller which spends all of its life outdoors and operates at a higher condenser fluid temperature. Air-cooled chillers can have a life time duration of 15 to 20 years.
Air-cooled chillers will have lower maintenance cost due to less components, and the fact that cooling towers used in water-cooled systems need water treatment and the chiller needs condenser tube cleaning.
This leaves air-cooled chillers less expensive to install and maintain, while water-cooled systems are more energy efficient.
Water-Cooled Chillers
Water-cooled chillers can be located anywhere in the building or on the roof in a mechanical penthouse. The chiller shouldn’t be located in the basement unless access is provided for replacement. Locating the chiller on the ground floor with a removal louver or large roll up door allows for easy replacement and access for tube pulls.
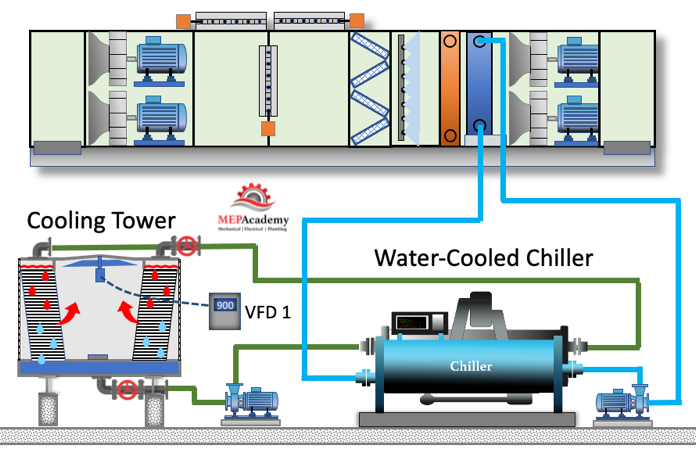
The chiller will need to be connected to a cooling tower for its heat rejection. This is an extra set of pipes leaving the chiller and connecting to the cooling tower outdoors. Cooling towers are mostly installed at ground level or on the roof.
The Chilled water from the chiller is circulated around the building with the use of Chilled Water Pumps. The chilled water will circulate to all the equipment requiring cooling, which includes Air Handlers, Fan Coils and Blower Coils.
As air from the rooms in the building pass over the chilled water coils, the heat will be absorbed by the chilled water circulating through the coils in this equipment.
The heat circulates from the room through the chilled water to the water-cooled chiller where the heat is transferred into the refrigerant circuit within the chiller. The refrigerant circuit moves this heat from the evaporator to the compressor where it is compressed from a low-pressure gas to a high-pressure gas in the condenser.
Water from the cooling tower will circulate through the water-cooled condenser of the chiller and absorb this heat causing the high-pressure gas to condense and turn into high pressure liquid.
The cooling tower water has now absorbed this heat and then rejects it to the atmosphere. (See our video on the explanation on how Cooling Towers work).
Air-Cooled Chillers
Air-cooled chillers are limited in size by some energy codes as they’re considered less energy efficient than water-cooled chillers. The air-cooled chiller rejects the heat absorbed from the building by blowing air from a fan over refrigerant circulating in the condenser coils.
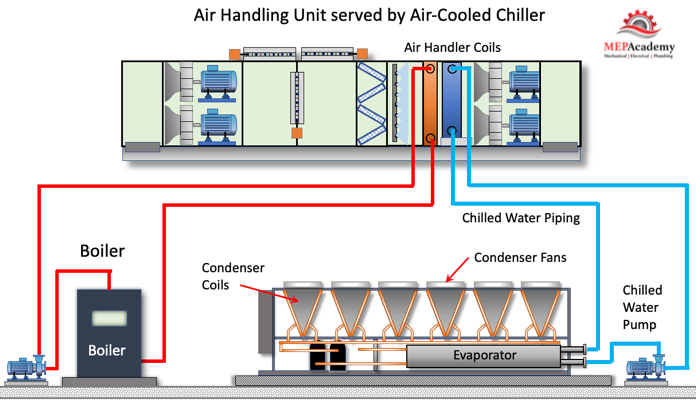
Air-cooled chillers are available from as small as 10-tons to as large as 600-tons. Air-cooled chillers can be order with factory installed pumps that can save on installation time.
When looking at aerial videos or images of buildings you can spot air-cooled chillers, as they’ll have a row of fans along the complete top of the chiller used for heat rejection.
Air-Cooled chillers can be ground mounted if there is space available. Consideration needs to be made for the noise generated by the condenser fans.
Water-Cooled Chiller Control Sequence of Operation
So, here’s a simple explanation of a control sequence working with the chiller, in this case the water-cooled chiller and cooling tower. Actual sequences of control can be very elaborate with the goal of optimizing energy efficiency included in the algorithms.
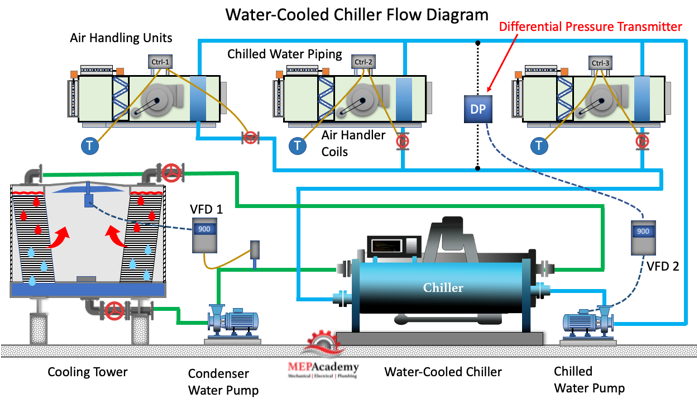
You may have a temperature sensor in the room asking for more cooling or less cooling. It’ll send a signal to the air handler controller, the controller will send an output signal to the 2-way control valve to open or close, and then the differential pressure transmitter will pick up those changes and send output signal to the VFD, which will either speed up or slow down the chilled water pump, increasing or decreasing the flow of chilled water based on the demand.
On the condenser water side you could have a temperature sensor in the condenser water supply piping, sensing the temperature. If the water is getting too cold because the chiller demand is low, than the fan will be adjusted to a lower speed, and that’s how it works with the chiller to optimize the tower.
Air-Cooled Chiller Control Sequence of Operation
The air-cooled chiller setup similar, but it doesn’t have to worry about the cooling tower. So, once again the temperature sensor in this space will send and input signal to the controller, and the controller will send an output signal to the 2-way control valve, whether to open or close, based on whether it needs more chilled water or less.
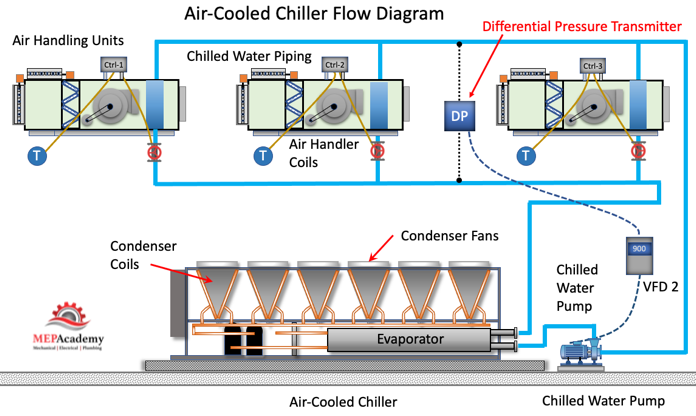
The differential pressure transmitter of course will sense that buildup of pressure if these valves are all closing, an this pump is still pumping at the same speed, this pressure is going to build up and that differential pressure will be set to reduce the speed because the pressure is increasing too much, which means the demand has dropped off, so it can save on the pump energy by reducing its speed.
Air Handling Units
The air handling unit has a chilled water coil and a fan that blows air over the cold coil before delivering it to the space. These differ from the Rooftop units that have the complete refrigerant circuit housed within the equipment. Air handling units cool the air by passing the warm room air over a coil that has chilled water circulating through it. The heat is absorbed by chilled water, whereas the rooftop units room air will be cooled by refrigerant circulating through the indoor coil.
See our video on Rooftop Units and our other video on Air Handling Units for a better understanding of these two systems.
The Air Handler will also use heating hot water or steam to heat the building, while the rooftop unit maybe a heat pump which uses a reverse refrigerant cycle for heating, or it may contain a gas furnace. Hot water or steam from a boiler will be sent to the air handlers heating coil to transfer heat from the coil to the room air passing over the coil.
Air handlers are available in much larger sizes than rooftop units, with custom air handlers up to 400,000 CFM.
Air handlers can be roof mounted or sit in a mechanical room on any floor in the building. Often many air handlers will serve a large building being scattered throughout the building, or one dedicated per floor, or one unit may serve the complete building. One of the main decisions is where to locate the air handling units while allowing space for sheet metal ductwork throughout the building to provide fresh air, relief air, return air and supply air.
Fan Coils and Blower Coils
Fan coils and blower coils are used for smaller spaces than what an air handling unit can cover. Fan coils can be horizontal hung or vertically stacked such as used in hotels. See our video on Fan Coils for a better understanding of these systems.
The fan coil is a miniature version of an air handler, but much less sophisticated and with fewer options. Fan coils serve much smaller areas than air handlers, and are manufactured with air volumes up to 4,000 CFM
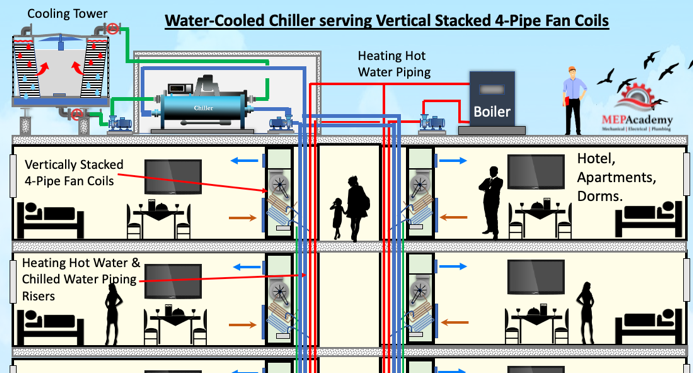
Fan coils are dedicated to a single zone, while air handling units can serve a single zone to a large quantity of zones. Another difference is that outside air or ventilation air is often provided by a separate system for the fan coil unit, while the air handling unit provides its own outside air. The fan coils are often not sized to handle the load for the ventilation requirements.
Some of the fan coils lack the capacity to handle better filtration options such as HEPA filters, UV Lighting or MERV 13 filters, this is due to lack of physical space or fan static pressure limits.
Often the fan coil is located in or above the room in the ceiling space which can cause the occupants to hear some fan noise. The air handler is located remotely so fan noise shouldn’t be an issue.
The fan coil can be constant or variable volume, using constant volume the fan coil can adjust the leaving air temperature, while with a VAV fan coil, the volume of air will be adjusted to meet the space temperature requirements.
Heat Recovery Chillers
With the focus on energy efficiency some chillers have the option of recovering the some of the heat that is normally rejected to the atmosphere. This recovered heat can be used for pre-heating of various systems.